TITANS OF NUCLEAR
A podcast featuring interviews with experts across technology, industry, economics, policy and more.
Latest Episode
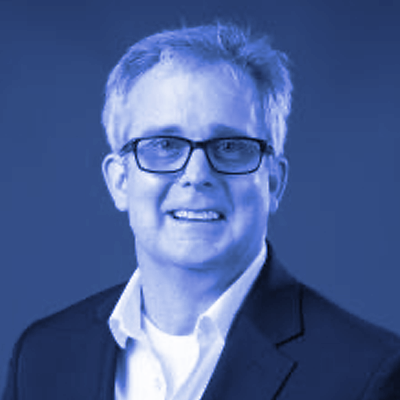
1) The beginning of Brian’s career and his time in the United States Navy as a diver, as well as what drew him to engineering and nuclear
2) Brian’s initial journey to Oregon State and all of the research projects he’s had a hand in since then
3) Fostering a passion for nuclear in the next generation of nuclear engineers and why the researchers as just as important as the research itself
4) What challenges and successes the nuclear industry will face in the coming years and how to form your individual opinion on nuclear energy
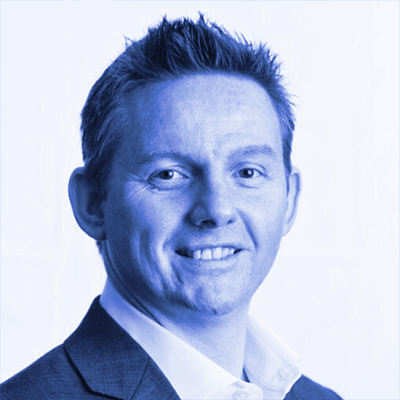
1) The new RAB finance model will attract long term investors to the UK’s nuclear industry
2) Nuclear investment is needed for the UK to reach the Net 0 Target of 2050
3) The Copy and Paste model decreases nuclear project risk
4) The importance of educating children at a young age about nuclear power
How a land rover began Tom’s nuclear journey (1:17)
1:17-8:29 (Tom describes how he first became interested in nuclear energy.)
Q. How did you get into the nuclear space?
A. Tom is from Liverpool, England and only got into nuclear engineering years after building a Land Rover with a friend. At the time, Tom worked in outdoor education teaching children to rock climb. Tom and a friend wanted to climb Mt. Kenya and decided to build a Land Rover to drive there from the UK. While Tom never drove the car outside of the UK, this spurred his original interest in engineering. Later, Tom got an engineering degree from Liverpool University and began working at an engineering firm in project engineering and management. Tom had always wanted to work in the energy sector and was able to work in the nuclear industry in the early 2000s on uranium enrichment plant projects. In 2008, Tom entered the nuclear industry full time as the UK advanced their new nuclear builds. Tom is now the Vice President for International Business Development at Assystem.
The UK’s new RAB financial model (8:31)
8:31-15:30 (Tom explains the history of the UK’s nuclear industry and the new RAB financing model.)
Q. What is the history of nuclear in the UK?
A. The UK nuclear industry began in the 1950s. The UK always collaborated with the US on matters of nuclear defense but went in different directions when developing domestic nuclear energy. The first fleet were Magnox reactors which lasted about 40 years and used non-enriched uranium. The UK then built 15 Advanced Gascall Reactors (AGR), 50% of which will be switched off in 2025. The UK currently has one Pressurized Water Reactor (PWR), which is what the US originally built. The UK is also testing fusion and high temperature reactors in the UK, France and internationally. The next advancement for the UK is building EPRs, which are the next generation of PWRs.
The UK recently privatized the nuclear sector and developed nuclear policy and financial mechanisms in the early 2000s to attract investors, utilities and vendors to the UK market. Current projects include the EDF and China National Group (CGN) partnership to build Hinkley Point C nuclear power station and the Sizewell Nuclear Power Station project, which is currently in the planning phase.
The UK government is about to launch the Regulatory Asset Based (RAB) financial model which will allow investors to draw down a profit before actual assets are generating an income. This will attract long term investors, such as pension funds. Investors will gain a small return at first and a better return once the power plant is switched on. The RAB model is necessary to generate new investment for the UK’s nuclear industry because projects can sometimes require tens of billions of UK pounds, which is difficult to secure.
Financial difficulty has caused some nuclear projects to be paused. The Contract for Difference (CFD) funding model was used to finance the Hinkley Point C power station which manages risk sufficiently to give EDF the confidence to build plans and hit milestones. This model will not be used for the Sizewell project, which is currently paused, because the amount of investment needed is too much for EDF to attract. GE Hitachi Nuclear Energy has also paused their nuclear project. After investing almost 2 billion UK pounds, they were unable to attract the right investors to secure the funding needed to begin construction.
Large reactors come with high capital costs, but can last 60-80 years and will generate low cost, low carbon electricity. It is difficult for the private sector to fund these projects and, due to projects overrunning their timeframes and budgets, institutional investors are nervous to get involved. The RAB model hopes to alleviate some of this concern and excite the investment market, ultimately moving UK nuclear projects forward.
Reaching the Net 0 Target of 2050 with Nuclear (15:31)
15:31-22:45 (Tom discusses the funds needed to support a nuclear project and the reasons why funders may pull out. He also notes his optimism of the UK government’s support of nuclear energy moving forward.)
Q. Is the largest segment of capital cost the construction of the plant or the licensing and testing?
A. There are two elements of cost: capital cost and cost of finance. Capital cost involves the costs associated with design, manufacturing, planning, licensing and construction. About 20% of capital cost is spent on planning while 80% is spent on construction. When large costs start to build, projects must secure investment.
Projects may end prior to construction. This is not due to the expense, but usually because of political reasons. In the UK, Hitachi needed to attract both investors and an operator to run the nuclear facility post construction. Due to the UK’s political environment, they were unable to do so.
Luckily, the UK government is beginning to understand the need for nuclear energy, especially in reaching the Net 0 Target of 2050. While the UK public support wind and solar, these renewable energies are unable to support the base load electricity. As the UK government gets rid of coal and decreases gas, they will need to develop the nuclear industry further to supply the UK’s electricity needs. Enabling investors is key to achieving this and the nuclear industry is confident in the UK government’s ability to do so.
Educating youngsters to increase the UK’s nuclear percentage (22:46)
22:46-26:56 (Tom discusses the current percentage of the UK’s energy that comes from nuclear power and why we need to increase this percentage. Tom also speaks about the importance of educating children about nuclear power.)
Q. What is the percentage of nuclear right now in the UK and where do you see this percentage going in the future?
A. The 15 reactors that EDF own and operate currently generate 20% of the UK’s electricity. With the electrification of cars and increased electronic device ownership, the demand for electricity in the UK will increase over the next 10 to 20 years. As the UK decreases coal and gas, wind and solar will not be enough to meet the demand alone, especially considering the intermittency issues associated with dark English winters. Nuclear power, therefore, needs to be part of the solution.
Tom remembers a school trip as a child to the Sellafield nuclear laboratory visitor center. This was part of a campaign to educate school children about nuclear power and radiation, which ended in the 1990s. EDF is beginning to open visitor centers to educate the public about the low risks and impacts of nuclear power. While governments currently only think about 5 years into the future, they should be planning for future generations when natural resources begin to run out. Because 97% of nuclear fuel is recyclable and lasts decades, nuclear power should be considered by governments. Educating at a young age will help increase public support of nuclear power as the UK government plans for future electricity sources.
Decreasing project risk with SMRs and the Copy and Paste model (26:57)
26:57-33:47 (Tom discusses the different roles he has undertaken in the nuclear sector. He also discusses the countries that he foresees as perfect opportunities for nuclear growth as well as the Copy and Paste model.)
Q. What sort of projects do you work on as International Business Development Manager?
A. Tom has spent the last 10 years working on UK nuclear plant life extensions, upgrades and new builds. On the international front, Tim acts as an ambassador for the UK in bilateral nuclear agreements intended to share nuclear learnings and technology. He has worked in Japan, the Middle East, Poland and Turkey.
Some developing countries present perfect opportunities for nuclear development. In some places, a lack of grid infrastructure that restricts their ability to support a large scale reactor are perfect candidates for SMRs. These small modular reactors are manufactured in factories and then shipped to the location. India, for example, has a huge population and a high energy demand. Nuclear power is the only option to provide sufficient energy without using coal. India should be able to scale their nuclear program over the next 10 to 20 years to be similar to that of China.
One way to increase efficiency and reduce risk is to use a Copy and Paste model. This is when two identical nuclear facilities are built, reducing learning curves and costs while keeping construction on schedule. However, different countries have different regulations, meaning the Copy and Paste model does not always work. A regulator may change aspects of an existing plan to meet safety standards. For instance, the UK has the ALARP system meaning risk should be as low as reasonably predictable while the US’s NRC takes a more prescriptive approach.
Assystem’s strategy for nuclear project success (33:48)
33:48-42:50 (Tom describes Assystem’s strategies of following the customer and acquiring partner companies. Tom also notes the difference between markets pulling and pushing nuclear power.)
Q. Does Assystem focus on optimization when there are new regulations?
A. Yes. Assystem works on the basic design for the new EPRs and detailed construction designs. Assystem is also working with Rolls-Royce to produce the conceptual design for a small PWR reactor.
Assystem finds new projects by following their customers. They are an independent engineering and project management company rather than a nuclear vendor or utility. Their goal is to understand the country they will be working in, meaning familiarizing themselves with the local supply chain, legislation, policy and existing nuclear dynamics. They form partnerships with engineering companies, construction companies and consultancies, sometimes acquiring the companies they partner with. An example of this is when Assystem acquired Envy, a planning and geotechnical engineering company in Turkey. When Assystem was working with the Turkish government to plan the Russian VVR reactor project, Assystem formed a partnership with Envy and in 2016, acquired the company. This is beneficial because Assystem can utilize both their skills in Turkey with the skills from the UK and France to successfully support the nuclear program. This move enabled Assystem to gain approval by the Turksih regulator to oversee the project. Later in Saudi Arabia, Assystem was able to win a nuclear development program contract because they had the geotechnical knowledge and skills from acquiring Envy. The nuclear sector is global, requiring partnerships to be formed with local companies, communities and governments. A successful project depends on understanding the interactions between all stakeholders.
For Assystem, it is easier to work in a market pulling nuclear energy rather than one that is pushing away from nuclear for political reasons. Political risk brings uncertainty as politics can change yearly. Tom notes South Africa, Egypt and Kenya as examples of markets pulling nuclear energy. While Germany represents a market pushing away from nuclear, Tom believes they will likely extend their existing fleet in the future. This is because Germany pushed wind and solar 10 years ago, but they are still relying on coal and their existing nuclear as these renewable energies have not produced what is needed. Additionally, they will need to decommission their plants at some point, affecting jobs. The German government may change their position on nuclear in the next 10 to 15 years.
Reducing the UK’s 30 year nuclear construction gap (42:51)
42:51-52:06 (Tim states that nuclear energy will be used alongside solar and wind. He also discusses how the RAB and Copy and Paste models will decrease the UK’s nuclear construction gap in the future.)
Q. Are you suggesting that nuclear will prove itself over wind and solar and other technologies that may come along?
A. No. Nuclear power will not push out wind and solar but will be used as well as them. Nuclear is low cost and low carbon and will provide the base energy load for up to 100 years.
Moving forward, the UK must factor in decommissioning and waste management plans into their planning applications to think about solutions to issues now. Additionally, the Copy and Paste model can be a game changer to increase safety and efficiency. This will require, however, engineers and scientists to understand that changing designs increases risk. Copy and Paste can decrease costs by 30% and increase investor confidence that a project will be on time and on budget.
There has been a huge gap in nuclear construction in the UK. The last reactor built was in 1995. Hinkley Point C is due to be operational in 2025. The RAB and Copy and Paste models should help reduce this gap in the future. Additionally, SMRs can help increase speed as they are built in controlled environments that are not subject to weather delays. The UK’s nuclear industry is moving towards one similar to that of the automotive industry: one of quick build and low risk.
Education is key to the future of nuclear (52:07)
52:07-59:16 (Tom explores how a nuclear incident may affect Copy and Paste model reactors. He also reiterates the importance of education at a young age in securing the future of nuclear for the UK and the world.)
Q. What if a Chernobyl-like accident were to occur, shutting down all Copy and Paste model reactors? How would we navigate this?
A. Nuclear incidents push the market back 10 years, forcing the industry to rebuild confidence. An incident like Chernobyl will not occur in the US, UK or France due to the jurisdictions in place. The Fukushima accident was caused by an earthquake and the following tsunami, not the actual reactor itself. The nuclear industry must continue to educate and be transparent with the public to build support.
Education focusing on the limited nuclear risks are also important. This education must begin with children to increase the public’s comfortability with radiation. This level of education is also important for inspiring the next generation to join the nuclear industry through global outreach programs. There is currently a skill gap in the industry as many undergraduate students today do not choose nuclear engineering as a focus. Efforts must be made to increase the appeal of the sector by making it an exciting opportunity from a young age. Additionally, governments and the nuclear industry must collaborate to educate the public on the need for nuclear power in addition to wind and solar energy for reaching a zero carbon target.
2) 4 most salient bullet points
(1) The new RAB finance model will attract long term investors to the UK’s nuclear industry
(2) Nuclear investment is needed for the UK to reach the Net 0 Target of 2050
(3) The Copy and Paste model decreases nuclear project risk
(4) The importance of educating children at a young age about nuclear power
3) Two quotes to use as episode teasers
(1) 25:17-25:55 “And we’re just starting to actually see EDF opening up its visitor centers again at site to start to educate the youngsters that it’s not a big issue, it’s not a Homer Simpson cartoon character and I think that education needs to happen and that’s a responsibility I think of both governments and the sector and the industry itself to make sure people are aware that this is actually a low risk technology and the impacts of nuclear power are minimal and we have engineered solutions that can cope with waste for decades and thousands of years to come really. So I think that educational piece is something to really take to the general public in the UK and it starts with the youngsters.”
(2) 45:18-45:59 “Companies that design and build nuclear power stations are full of engineers. And regulators who regulate the build of nuclear power stations are full of engineers and scientists. And they tend to love to innovate and change and make things better. And one would argue that doing that inherently makes things safer. And in reality, and I think this is the challenge that we need to convince our engineers in those companies and in our regulator, change in a nuclear power station actually increases risk because you’re asking engineers, manufacturers, designers to do something new for the first time."
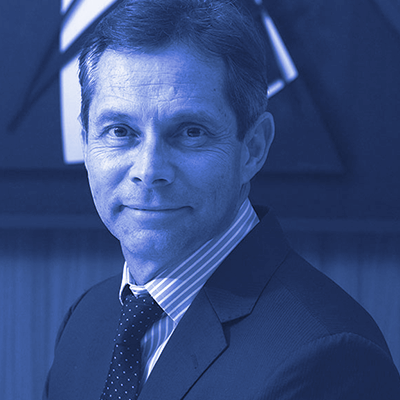
1) Assystem’s role in France’s nuclear industry
2) The importance of mixed engineering teams when designing, constructing and commissioning nuclear power facilities
3) Regulating fusion as a means to gain public support for nuclear power
4) The role of ITER in the future of nuclear energy
Bernard’s role in reinventing nuclear (0:55)
0:55-7:43 (Bernard discusses his journey to becoming the Nuclear Business Development Manager for Assystem. He also provides a brief overview of France’s nuclear industry history.)
Q. How did you get into the nuclear space?
A. Bernard is from the South of France where he attended engineering school. His first role after graduating was as a trainee building a nuclear facility. Bernard then went on to become involved in nonnuclear construction projects, including infrastructure projects in Saudi Arabia, in the French steel industry and in the automotive sector. He then moved into managerial and operational roles and eventually into business development. He returned to nuclear in the early 2000s with a variety of viewpoints and is now the Nuclear Business Development Manager for Assystem.
In the mid 1960s, Assystem was created to support architect engineers that needed to license new nuclear facilities. The Autorité de Sûreté Nucléaire (ASN), France’s nuclear safety authority and strong regulation body, requires operational licenses and several thousand verification tests during a facility’s commision phase before a plant can become operational. In the 1990s, the construction of the initial French nuclear facilities was about to be completed. Assystem shifted away from construction to help move these facilities into full operation by supporting operation, optimization and maintenance. Today, the nuclear industry is strong in France. Building new nuclear facilities, however, is difficult. Assystem’s current goal is to focus on reinventing methodologies to improve the nuclear industry’s performance.
Improving nuclear construction efficiency (7:44)
7:44-17:44 (Bernard discusses how new ways of engineering with mixed teams are key to achieving efficient and cost effective nuclear construction. Bernard also mentions the importance of designing nuclear facilities with the construction and commissioning phases in mind and touches on the differences between US and French engineering.)
Q. What are some of the ways that you see construction becoming more efficient and more cost effective?
A. More modular construction creates more efficiency and is more cost effective than large reactors. Modular construction is not the only way to achieve this, however. Digital tools, new ways of engineering and creating a strong link between the engineering and construction phases are also key. Continual building and rebuilding without stopping a project will also lead to more efficiency and cost effectiveness.
Connecting design engineers with construction engineers is also important. Creating the best design possible requires considering the construction and commissioning phases during the design phase. Mixed teams of nuclear engineers, construction engineers and people involved in commissioning will have overall better performance that teams of only nuclear engineers.
The US and French nuclear industries have some differing approaches to development. While the US nuclear industry has separate engineering and operation companies, French companies, such as EDF, want to both design and operate facilities. Assystem supports EDF engineers in doing this, not only helping to design the nuclear power plant, but also the nuclear support buildings, such as the waste treatment building. Additionally, unlike US universities, France has engineering schools where students learn broadly about engineering. Engineers only specialize after graduating. Bernard, for instance, was not trained as a commissioning engineer, but broadly wanted to build something to help the world.
In support of nuclear fusion (17:45)
17:45-27:32 (Bernard describes the difference between nuclear fusion and fission and the ITER project. Bernard states why it is important to fund both nuclear fusion and fission reactors.)
Q. What exactly is fusion and why is it difficult to make it commercial?
A. Broadly, fusion reactors are used for research and development while fission reactors are used to generate power. Fusion is complex and difficult to explain and research has progressed slowly due to the large fusion research reactors needed.
ITER is a nuclear fusion project with a unique international collaboration between 7 partners: The US, China, South Korea, Russia, Japan, India and Europe. The goal is to share fusion funding and knowledge and to establish a network for next phase fusion reactor building. ITER is the largest test reactor in the world and is used to understand how to manage and control fusion reactors. It is also used to understand how to improve fusion reactor technology to eventually produce electricity.
ITER is a step towards producing fusion energy by the end of the century. Fusion is safer and lower waste than fission because sea water, not uranium is needed to power the reactor. Fusion could be used to generate infinite energy and has already been featured in popular culture, such as in Star Wars.
Because fusion is a long term commitment, it may make more sense to focus on fission to address climate change now. However, it is important to distribute resources because fusion and fission are different projects. Fission reactors need improvements to increase construction speed and to remain in budget. Fusion requires investment because it is the energy of the future. Both require a lot of money, but are both critical in the immediate and distant future of nuclear energy.
Gaining nuclear support through regulation (27:33)
27:33-39:28 (Bernard discusses the role government plays in nuclear projects and the need for fusion regulation.)
Q. Do you think it is better when projects are supported by the government?
A. Nuclear projects are costly and take time and are therefore not ready for full private investment. Nuclear energy is also strongly linked to policy because of states’ electricity and development interests. Security, safety and improvements are additional reasons for government involvement in nuclear projects. Nuclear regulators, which are independent of governments, also play a strong role in projects. While this can slow down even privately managed projects, they are necessary.
ITER will be the first nuclear fusion facility to be regulated. Smaller fusion reactors are not classified as nuclear facilities and are therefore not regulated. Because nuclear has a rocky history, regulations can bring more comfort to people by ensuring them that a facility is safe and well operated.
Regulating fusion is questioned, but Bernard states why it is necessary. Research and development into fusion is needed because, unlike fission, fusion does not require uranium, which will be expended in about 150 years. While regulation may influence the public to think all nuclear power has a degree of danger, it also ensures the public that facilities are safe. Public support is crucial in moving towards fusion energy and the ultimate future of nuclear power. It is therefore worth the costs associated with regulation.
Reaching goals through international collaboration (39:29)
39:29-50:29 (Bernard discusses Assystem’s role in ITER. He also mentions if ITER is on track to achieve goals and the collaborative work environment behind ITER.)
Q. What is Assystem’s role in the ITER project?
A. ITER was established in 2005 and Assystem’s role of nuclear safety engineering support began in 2006. Assystem is involved in engineering and designing key components of the reactor, but also in architect engineering of the buildings in the facility. They are also in charge of construction, meaning providing supervision, coordination, inspection and an evaluation of the full facility.
This is a long term commitment, as ITER will begin the First Plasma phase in 2025 and reach full power in 2035. The primary goal of ITER is to demonstrate the success of a nuclear fusion reactor. ITER is currently on track to meet goals.
The collaboration in this large, international organization is key to reaching these goals. This includes Assystem’s young graduate program that trains graduates in nuclear fusion. Assystem believes that investing in people is required for long term project support. Many students come from a construction or engineering background which supports the idea that bringing together non-nuclear backgrounds creates more open minds and better conditions to work together. Momentum and Engage are two teams that set an example of how different expertise can be brought together on an international level to not only push ITER’s research and development, but also train people on various languages and cultures. This creates an exciting and interesting work environment for the ITER project.
Using fusion to reach a galaxy far, far away (50:30)
50:30-55:18 (Bernard discusses the following phases in fusion energy and what he believes is the future in nuclear power.)
Q. Are you able to develop commercial models for fusion in France or must ITER first be completed?
A. After ITER is active in 2035, it will be used as a research reactor for 10 years. In 2045, ITER will then be decommissioned as the reactor is designed only to operate for 10 years. The next phase of nuclear fusion is to produce electricity. Between 2050 and 2080, DEMO will be built which will produce fusion energy. The following industrial phase is projected to begin in 2100.
Bernard strongly believes that a commercial phase for fusion reactors is less than 80 years away. ITER is a key phase in fusion development and is comparable to landing on the Moon. Bernard sees a future of using nuclear fusion energy to power space travel and exploration.
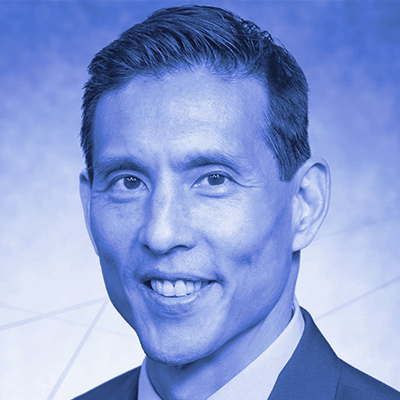
1) The founding principles of nuclear regulation
2) The NRC’s new modernized approach to risk
3) Licensing advanced reactors
4) The opportunity for the NRC in the future of nuclear
Becoming Director of the NRR (2:40)
2:40-9:46 (Ho explains his path to becoming the Director of the Office of New Reactor Regulation at the NRC.)
Q. Your dad was a nuclear welder, is that right?
A. Ho Neih’s father was a nuclear welder in North Easterly US. While growing up in New York, Ho’s father steered him towards science and technology, encouraging him to study engineering at the United States Merchant Marine Academy. After graduating, Ho worked on a prototype plant for the navy nuclear program before becoming a resident inspector for the Nuclear Regulatory Commission (NRC). He is now the Director of the Office of New Reactor Regulation (NRR).
While Ho’s engineering education gave him an objective mindset, the NRC and attending business school taught him that regulation is not black and white. Early in his career, he was able to work under a former NRC chairman where he learned how public policy is formed. This gave him insight into the bigger nuclear industry picture.
It is fairly common for employees to take on different positions within the NRC. Taking on different assignments in different program offices gives employees a chance to see things in a different light. For example, Ho worked in the Office of Nuclear Security and Incident Response after the September 11th terrorist attacks in New York City. This enabled Ho to look at nuclear facilities from a protection and emergency preparedness viewpoint rather than from an inspection and safety systems perspective.
The principles of nuclear regulation (9:47)
9:47-16:07 (Ho explains the primary principles behind nuclear regulations.)
Q. What are the founding principles of nuclear regulations?
A. The CRF10 regulation book is based on the idea of reasonable assurance of adequate protection. The agency has never defined adequate protection because it allows for engineering judgement and Defense in Depth, which are the multiple layers of protection put in place. Adequate protection does not mean zero risk, but rather protects people and the environment from radioactive material which could pose a hazard.
The NRC is going through a major evolution to become a modern risk informed regulator. The primary focus is to understand what risk-informed and reasonable assurance mean. In practice, making a decision about a regulatory action comes down to a concern about a risk or exposure to a hazard. Three questions are asked when making regulatory decisions: what can go wrong; how likely is it; what are the consequences. The probabilistic risk assessment technology gives insights into how likely an event is to occur and the potential consequences. These are both used to help inform NRC decisions, however, decisions are not based on numbers alone. Other factors, such as the deterministic criteria in regulations, material quality, Defense in Depth in place, mitigation strategies, and performance monitoring, are also taken into consideration.
Adopting Silicon Valley’s view on risk (16:08)
16:08-20:22 (Ho explains the need for the NRC to take on more risk.)
Q. As part of this transformation, are people allowed to bring out of the box thinking into the mix?
A. Yes. Another element of risk is being able to take risks. The NRC does not regulate to 0 risk as there may be some risk associated with every decision. The NRC must overcome the fear of risk, meaning out of the box thinking is important. Ho visited with innovative technology companies to understand how startups achieve success in Silicon Valley. He learned that they have a strong bias towards risk taking. They understand what the risks are, the probability of failure, how to mitigate the risk and then take the risk anyway. This approach to risk is known as “fail often, fail early.” The NRC needs to challenge itself because there is no risk is repeating what has always been done. Becoming more efficient requires the NRC to take on the risk of questioning previous ways of doing.
Flexibility with Defense in Depth (20:23)
20:23-26:07 (Ho explains the need for Defense in Depth. He also explains the five aspects that the NRC uses to determine risk.)
Q. Would you be willing to hear an argument against Defense in Depth?
A. Ho is open to hearing any argument. The NRC must be flexible and listen to alternatives about how to meet criteria. Defense in Depth, however, is internationally recognized. Ho understands that innovation and technology can improve safety, as seen in the automotive industry, but believes Defense in Depth is still needed in nuclear. The NRC can be flexible about this, however. Recently, the NRC was looking into a Small Modular Reactor (SMR) design where the applicant wanted to apply single failure criteria to a single valve. The NRC staff determined that the overall consequences were sufficiently low that Defense in Depth was not needed for this particular valve.
The NRC look into five aspects when determining the safety of a nuclear system: what are the regulation requirements, the Defense in Depth in place, safety margins, quantitative risk information and the type of performance monitoring that can be carried out. Ho notes that judgement must be applied here because nuclear regulation is not black and white and decreasing risk further may not always be in the public’s interest because of the cost associated with some decisions. There is therefore a tradeoff between the five aspects the NRC uses to determine risk and safety.
Making plants safer after Fukushima and 9/11 (26:08)
26:08-32:09 (Ho discusses the actions taken to make plants safer after Fukushima and the September 11th terrorist attacks.)
Q. Have we readjusted our notion of consequence as we’ve learned more from the various nuclear accidents that have occured?
A. There are international committees dedicated to radiation protection and dose levels. The industry is learning from Fukushima. Even though this was a rare accident caused by natural events, the industry learned that this type of accident can occur and thus some level of protection must be in place to prevent a similar accident occurring again. One measure put in place is the portable equipment to supply cooling water and power supplies to a facility in the event of an extreme accident. This equipment is located onsite and offsite at warehouses that can be delivered to any plant within the US in 24 hours. Another example is after the September 11 attacks, the NRC issued orders for nuclear plants to increase their level of security and to have portable equipment in place in the case of plant loss due to fires or explosions.
Modernizing the licensing process (32:10)
32:10-41:37 (Ho explains the licensing process for new reactor designs. He also discusses the new steps the NRC is taking to modernize the licensing process.)
Q. When a new technology wants to come to the NRC with a new idea, what’s the process for them to do so?
A. Companies with new technologies are already coming to the NRC. Non-light water designs are currently in pre-application discussions to understand the licensing process. With advanced reactors, each potential applicant will do their own review of licensing strategies and follow the process that makes the most sense for them. However, both licensing strategies (Part 50 and Part 52) were created with the traditional light water reactor designs in mind, meaning new designs require applicants to file exceptions no matter the licensing strategy chosen. The NRC is looking at different approaches to understand the new advanced reactor designs and the types of events that must be analyzed to determine safety criteria.
The NRC is also asking themselves how to do reviews differently. Ho notes that it makes little sense to take an advanced reactor design with better safety features and force it to fit the normal way of reviewing plants. The reviewing strategy of big light water reactors was to break the licensing process into components and have experts review each part separately. The new way of licensing will bring together fuel and electrical experts to take a more integrated review of advanced reactor designs.
The NRC is also looking to decrease the amount of time it takes for a plant to go through the licensing process. The Nuclear Energy Innovation and Modernization Act places requirements on the NRC to decrease the licensing process to 24 months rather than 4 to 5 years. Ho is challenging his team to look at the product that is actually being produced rather than reading through large amounts of materials and producing long reports. He believes it is most important to spend time on the issues that matter most to safety and is therefore important to question if the resources spent on studying a particular safety issue will improve safety of the plants today.
Decreasing regulations on new reactor designs (41:38)
41:38-50:21 (Ho explains how the NRC is approaching new licensing requirements for new plant designs.)
Q. Decreasing regulation on low risk drones enabled commercial innovation to grow. Can there be an argument made here where we draw a threshold for research sized reactors and decrease regulation, creating a technological boom for the industry?
A. The innovation cycle leads to further improvements in other areas. For nuclear in the advanced reactor area, there are some basic requirements, such as site boundary dose requirements. For light water reactors, the dose requirement is very prescriptive, but there may be other driving factors for advanced designs. The NRC is therefore paving the way to enable plants to be licensed using different criteria than the large light water reactor designs.
The NRC is thinking about setting boundaries that would decrease the need for regulation based on the low risk that some designs present. For example, some designs eliminate the need for operators, which would decrease the need for operator safety regulations. This challenges the NRC to leave behind old paradigms, such as the one that a nuclear plant must have operators in a control room. The new designs use the pre-application discussions to understand the type of regulatory exceptions they may seek from the NRC. The NRC may also use this time to understand what modeling they will need to see to undertake a safety review of a new design.
The future of the NRC (50:21)
50:21-55:53 (Ho discusses the importance of the NRC and the NRC’s future.)
Q. What is the future for the NRC?
A. Advanced reactors present an incredible opportunity for the NRC. The US and Canada have partnered on regulatory reviews of advanced reactors, leveraging their combined knowledge. The role of the NRC is not to promote nuclear, but to ensure the safety of Americans through regulation. The NRC is important because it is the fundamental enabler for safe innovation and growth in the nuclear sector. The NRC has been criticized in the past for not being very risk-informed and for being inflexible, but Ho is excited for a new NRC which takes on risk and out of the box thinking to modernize the regulation process. Ho is thinking of the future leaders of the NRC who come from the generation that grew up in the digital age and are focused on finding meaningful work. Ho believes making possible safe nuclear technologies can attract this new generation. Creating a new mindset is the start of an exciting future for the NRC.
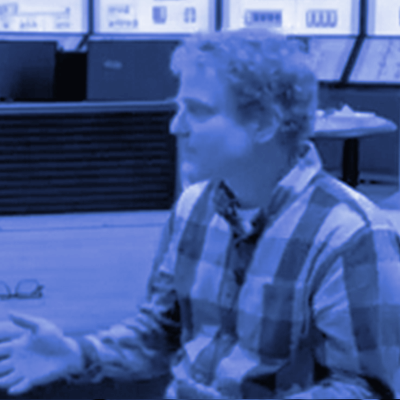
1) How working with locals during the Embalse Life Extension Project helped secure the future of nuclear power in Argentinian communities
2) The importance of refurbishments and how SNC Lavalin is learning from each CANDU refurbishment project
3) Tim's work as Director of Field Services in maintaining and operating CANDU reactors for longevity
4) How life extensions stack up to new builds and directions the nuclear industry can take in regards to each
1) How did you get into the Nuclear Field? 0:27
Tim Freeman is the Project Director at the Embalse Life Extension Project at SNC-
Lavalin. He has worked in several countries around the world as is currently based in
Ontario, Canada.
Tim joined the SNC-Lavalin lab around 12 years ago. Previously, he’d worked in
machine designed at smaller companies building components for automobiles and
medical devices. When approached about joining the nuclear industry, Tim jumped at
the opportunity.
Before joining the industry Tim didn’t know much about nuclear and hadn’t aspired to
become a nuclear mechanical engineer. In his work at SNC-Lavalin, Tim has led groups
in tooling-design for the delivery of the retube tooling set. Tim says it’s not dissimilar to
his previous work in industrial automation.
The retube tooling set applies standard mechanical principles tied with automation and
controls. Since Tim works on disabled nuclear reactors, his work does not require the
same level of safety controls use in operating nuclear plants.
Tim is continually impressed by the nuclear industry’s ability to adapt and build upon
other types of expertise such as the automation and automotive industries. Those
industries were on a down turn at the same time nuclear was on the rise. Therefore, Tim
says the nuclear industry has benefited from the existing knowledge base of mechanical
engineers from the automation and automotive industries.
2) Can you tell us about the Embalse Nuclear Plant in Argentina? 6:20
Tim and his team have recently completed the refurbishment and restart of the Embalse
CANDU-6 plant. The plant is located about two hours south of Cordoba, Argentina.
Cordoba is a central point of the automotive industry in Argentina. That project benefited
from local programmers who are experienced in machine design and building. The local
experts have the knowledge and experience to maintain and use the tools that Tim’s lab
creates in Canada and ships to Argentina.
The Embalse Nuclear Plant leveraged local experience to provide the majority of the
jobs on the project. It is important for Argentina and other countries to be able to
integrate local industries and gain the confidence to build and refurbish more nuclear
plants in the future.
Tim says almost every country aims to be internally self sufficient when it comes to
building and refurbishing nuclear plants. He says Argentina is staying true to this goal
by having about 95-98 percent local workers out of 4,000 workers on site. Select
experts from out of country and some specially sourced materials had to be imported.
But otherwise the production of reactor components was done locally to promote and
develop the local nuclear industry.
The Embalse Nuclear Plant refurbishment provided stable work for many Argentinians
including for the 800 or so permanent plant staff. Tim says the economy of the entire
valley has been bolstered by the project and a solid foundation for future growth. The
original plant was built in the 1970s, with the recent retube, Tim thinks there is potential
for 30 more years of plant operation with the possibility of a second or third retube down
the line. Providing the local community up to 90 years of continuous employment in a
high tech sector that produces clean, reliable power.
3) Was working in Argentina on the refurbishment different than working on
Darlington? 12:50
Tim has worked on the Bruce A Restart Refurbishment Project, the Darlington
Refurbishment Project and most recently in Embalse. He has also visited many other
refurbishment sites. Tim says there are differences, of course, but also many
commonalities including strong nuclear safety cultures and knowledgeable staff.
In Argentina, Tim says there are unique aspects of nuclear culture including a highly
educated local population who were qualified and capable. This was important because
the retubing is the core of a CANDU refurbishment project, meaning it is effectively a
production job.
At Embalse there are 380 fuel channels (and 480 at Darlington, but basically the same
thing as Embalse, according to Tim). Once workers have the tools to operate the first
channel, it simply requires repetition to remove the rest of the components from the
remaining fuel channels. Once the vessel has had all of the fuel channels removed,
workers can go in with radiation tolerant cameras to do an inspection. The cameras
inspect the insides of the empty vessel that is almost impossible to inspect otherwise
during assembly or operation. At Embalse, the inspection found the vessel to be clean
and in pristine condition.
The vessel is then reassembled with new components to effectively create a new
reactor. Finally, carbon steel pipe “feeders” spanning from one and a half inches in
diameter to three and a half inches diameter. Each fuel channel is fed on either side by
a pair of feeders that connect to a common header up above.
At Embalse and unique to CANDU plants, the steam generators were also replaced. It
was challenging and a first of its kind, according to Tim. Overall, the project progressed
exceedingly well and almost on plan and on budget.
4) Why replace the steam generators? 17:37
In the case of Embalse, there were challenges with corrosion issues in the internal
components, unique to that plant. To extend the life of the Embalse Nuclear Plant, the
steam generators had to be replaced. Tim says most CANDU plants will not require this
extra step at this point.
Embalse was the third plant to undergo this life extension project; previously one
occurred in Korea and another in Canada. Darlington has since been added to the list.
Each refurbishment comes with lessons learned about retubing that can be applied to
the next project. The Embalse Refurbishment Project benefited from previous
knowledge collected during the Korean and Canadian refurbishments, and will continue
to aid in future refurbishments. Refurbishments are essential to the future of nuclear
plants.
5) Have you encountered any setbacks during the past three refurbishment
projects that you’re still having trouble solving? 22:22
No, says Tim. At this point there has not been a technical challenge that the nuclear
field has not been able to overcome. Having done it three times on the CANDU-6 and
three times on the Bruce and Darlington configuration, there is a fairly high level of
predictability in the retubing process. Tim says the most complex and unpredictable
issues tend to be scheduling and costs. Getting the basic processes in control and
driving down the weld failure rate is essential to refurbishment projects.
6) Has the post-Fukushima era changed the process of refurbishments? 30:10
The retubing process has not been affected. But there are more safety requirements
that have been implemented to look for additional redundancy or examine areas initially
not considered potential threats during the 1970s.
The refurbishment process is often disconnected to other upgrade initiatives occurring
post-Fukushima. Those upgrades are required either way; therefore refurbishments do
not always fall on the same timeline was essential safety upgrades.
7) Now that Embalse Refurbishment Project is finished, what’s next for you?
33:47
There is a lot of work for Tim at home office. He’s phasing into his role as Director of
Project Management Office of Field Services. This office does work all around the
world, but mostly in Ontario, Canada. His goal is to support the long life of the CANDU
community in maintaining and operating rectors through inspections.
Tim partners closely with key clients and his team responds quickly to outage
requirements and outage schedules all around the world. He manages a core team of
experienced technicians and engineers as well as equipment that can be deployed for
specialized non-destructive evaluation techniques.
8) Can you talk more about the CANDU community? 38:24
Tim is a strong believer in CANDU refurbishment as a method of reliable, safe power.
He doesn’t think there is a viable replacement or alternative to CANDU power. CANDU
plants operate on a different life expectancy timeline than other nuclear plants. Most
plants approach regulators based on ten to 20 year life expectancy campaigns. Yet
CANDU approaches refurbishment with the goal of 30 plus 30 and so on.
Tim feels it is important to approach refurbishment in a way that is reliable and safe.
Especially since building new nuclear plants often hits a wall of unpredictable costs and
scheduling and general acceptance. Nuclear refurbishment is predictable, builds on
what is known and accepted in a community, and keeps the operating supply chain
intact. Tim would like to see the next generation of CANDU reactors built, but until then
he wants to promote nuclear refurbishment as a viable alternative.
Refurbishment is often branded as life extension projects. From public perception Tim
thinks it’s better that the plants aren’t brand new plant because brand new plants come
unpredictable risks and uncertainty that things aren’t going to operate as designed.
Whereas, which refurbish plants, the community has more certainty and trust in a plant
that has already been operating for 30 years.
Tim describes this example like a classic car. If someone has a classic car, the engine
might become tired and need an overhaul or maybe even a complete engine rebuild.
But other than the engine, the rest of the classic car is certified and replaceable. Versus
a brand new car off the line, with those Tim says there’s a combination of maybe “they
don’t build them like they used to,” as some people sometimes say about cars, and also
sometimes you get a lemon. Public perception often sides with predictable results.
Especially with plant staff, engineers and operators, they know that plant inside and out
and they are experts on the equipment. It’s better to give back a mostly rebuilt version,
rather than something new and different.
9) Do you have any advice for your children to reflect on in the future about the
modern nuclear field? 47:02
Tim says nuclear may not be perfect. But the burning of fossil fuels is contributing to
climate change. Nuclear power is the best alternative, better than hydro or renewables.
It is important that we don’t allow nuclear power plants to be decommissioned.
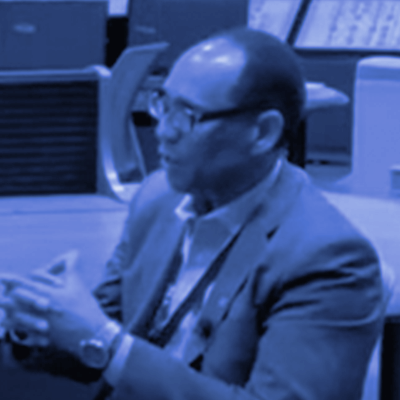
1) Ruben's early education in nuclear engineering during the Chernobyl incident
2) The importance of educating the young generations in nuclear to be engaged in the next wave of nuclear designs
3) Directions that SNC Lavalin is taking towards advanced technologies such as small modular reactors
4) An innovation drive approach to the future of nuclear power for generations to come
From Cuba to Moscow (0:26)
(0:26-5:49) Rubin explains how it was born in Cuba and attended college in Russia.
Q. You attended university in Moscow?
(0:26) Rubin Oris Valiente is the Vice President of Nuclear Steam Plant Engineering at SNC-Lavalin. He was born in Cuba when it had close ties to the Soviet Union. He received a scholarship to study nuclear engineering in Russia; he ended up living there for 10 years.
Q. You were in school in Russia when Chernobyl happened?
(1:59) During his third year of college Rubin remembers people coming and asking for volunteers to help clean up. Rubin initially volunteered, but after receiving messages from his Embassy and his professors about the scale of the incident, he and the other students passed.
Q. How did that change your view on nuclear?
(3:10) Chernobyl didn’t change Rubin’s views on nuclear; he still recognized that it is a much-needed industry. However, it did make him realize that the nuclear field needed more than just engineers to survive. After Chernobyl safety culture became more prevalent and interested in the field waned.
The Renaissance of Nuclear (5:50)
(5:50-19:19) Rubin discusses the resurgence of nuclear and how he’s preparing to pass the torch on to future generations.
Q. Is nuclear making a comeback?
(5:50) According to Rubin, nuclear has had two renaissance movements. The first, in 2010, saw a resurgence in nuclear until Fukushima happened. The field again suffered from a decline until recently, when Rubin says it became cool again.
Q. You’re in a great position of power during this most recent renaissance of nuclear.
(7:25) Rubin wants to contribute to keeping nuclear going. When he first moved to Canada, he realized there was a generation gap between different nuclear engineering roles. Rubin is trying to prepare the industry for when his generation retires, and younger people follow in their footsteps. He wants to design something interesting enough that future generations will want to carry the torch.
Q. Do most universities in Canada have nuclear programs?
(11:00) Rubin says not, and that it needs to be addressed through advertising the opportunities available to people once they enter the field. Currently, he knows of four or five universities that carry the nuclear engineering program, but that is not enough new educated members of the workforce during this renaissance of nuclear among all of the ongoing refurbishment projects. Rubin thinks the nuclear field needs to do a better job of educating the public about the benefits and possibilities of nuclear.
Q. What are some of the new and emerging technologies you’re working on?
(13:50) SNC-Lavalin has improved a new reactor design that is up to date with regulation standards and they are currently marketing it globally. SNC-Lavalin is also advertising their designs to investors, the public, and everyone to see.
Nuclear Around the World (19:20)
(19:20-27:26) Rubin discusses the nuclear industry and global differences and applications of technology.
Q. On a global scale, where do you see SMR reactors being used as compared to CANDU reactors?
(19:20) Advanced small modular reactors (SMR) are useful because they can go in remote locations, such as remote military bases, or isolated mining facilities. Small utilities that don’t want to produce a lot of capital all at once can also benefit from SMR reactors.
Q. Tell me more about your role as the Vice President of Nuclear Steam Plant Engineering at SNC-Lavalin.
(21:49) While Rubin doesn’t determine how much time is spent focusing on one type of reactor over another, he does determine how many engineers are working on a given project. He is the “Central Bank of Engineering.”
Q. What are some of the similarities and differences in training the global nuclear workforce?
(23:30) On the global scale, Rubin thinks the western world is blessed by the standards of safety and level of regulations society demands. Accidents at nuclear plants do not happen very often and the field has years of experience without any incidents. Rubin believes the nuclear industry has kept the highest standards of safety, more so than almost any other field.
Future of Nuclear (27:07)
(27:07-39:00) Rubin discusses the future at SNC-Lavalin and in his own career.
Q. Do you think engineering curriculum needs to change to make students more aware of newer technologies?
(27:07) Rubin thinks it’s a combination of curriculum changes and on the job learning. He believes that the first step is getting students excited about nuclear and the bright future of the industry.
Q. Do you think it’s financially feasible to continue to produce new nuclear technology?
(28:25) Rubin thinks the industry should continue to innovate and not just stick to one reactor design for the next 20 years. He also recognizes that eventually the industry will choose the best path. He’s already seen several designs he thinks will saturate the industry. And ones that aren’t mature enough, Rubin thinks will not move forward. He also believes that there will be another evolution of nuclear in 20 years with all new types of technology. Rubin believes humanity is constantly striving for the next level of innovation. He doesn’t think that focusing only on the one design will work, since it’s difficult to get everyone to agree on any one thing.
Q. What is SNC-Lavalin’s focus on the use of nuclear?
(32:50) Rubin says SNC-Lavalin eliminates a lot of barriers by using uranium fuels in reactors. They also have the ability to create and harvest isotopes. Recently, SNC-Lavalin helped a utility company to create isotopes. They’re focus is to improve the reactor design they have and help the SMR engineers improve their skills and training.
Q. What mark do you hope to leave on the nuclear industry?
(36:48) Rubin’s legacy wish is to leave behind people who are capable of continuing to care for the projects he started. He is also open to traveling to more countries to see how their nuclear industries work. Rubin likes to see the results of what he’s designed.
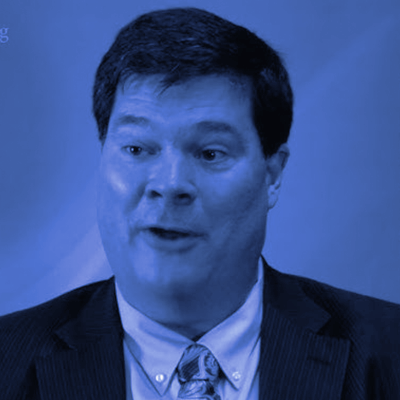
1) What Robert learned from working for ten years on maintenance issues at nuclear power plants
2) Innovation which guided the design of equipment testing devices and life extension projects
3) Shipping tooling systems to perform refurbishment processes on CANDU reactors worldwide
4) How innovations in automation and advances in technology will help save money and time on retube outages
Starting Out in Nuclear (0:52)
(0:52-15:46) Robert explains how he first became interested in nuclear while studying mechanical engineering and his early career.
What did you study in school?
(0:52) Robert Mallozzi is the Regional Technology Director of Retubing, Maintenance, and Inspection at SNC-Lavalin. During college he studied mechanical engineering at McMaster University in Ontario, Canada. He also has his master’s degree in mechanical engineering.
Why did you get your master’s degree?
(1:09) During undergrad, Robert worked on nuclear research in the labs. When he was approached by a professor to continue his research with a master’s degree he thought it seemed like the right move for him. He even out to tour a real reactor as a student. The pool-bed type of reactor is still being used at McMaster University.
Walk me through your career.
(3:29) Robert started his career working on steam generators and stress analysis. For the next decade of his career Robert worked in inspections and performed maintenance and repairs on reactors. During that time he traveled to all of the CANDU sites and lead the teams performing inspections and repairs. A lot of the issues he dealt with were the replacement of components that weren’t meant to be replaced.
What kind of training did you have to go through?
(10:34) First, Robert went through training on the reactors themselves and learned about the components and systems. He also went through extensive safety training for zoning and hazards.
Inspecting and Retubing CANDU Reactors (16:58)
(16:58-20:59) Robert explains his background as a CANDU reactor inspector.
How frequently do you conduct inspections?
(16:58) Depending on the component and reactor, inspections take place every three or so years. Sometimes regulatory requirements need more frequent inspections. Some components will be inspected every year, depending on the life of the reactor, history, and the regulatory requirements.
Do you inspect reactors more as they get older?
(17:00) Typically, yes. The older the reactor gets and the closer it gets to the end of its life means it needs to be monitored more frequently. CANDU reactors have a 25 year first life. Then they go through the process of refurbishment or retubing. This can generally extend the reactor’s life about another 25 years. However, this 25 plus 25 operating life was not the original intent for CANDU reactors.
Refurbishing Nuclear
(21:00-47:13) Robert describes the process and timeline of refurbishment projects.
Why was refurbishment not part of the original CANDU design?
(21:00) Robert wasn’t around during the CANDU design process, but he thinks that the technology for refurbishment is so innovative that it just didn’t exist back when CANDU reactors were first created. For example, refurbishment includes a lot of robotics. There has also been technology invented to reduce the volume of the old components so smaller volumes of radioactive components have to be put into long term storage.
After your decade working in inspections, what did you do next?
(23:54) Next, Robert landed in New Brunswick working on the refurbishment of the CANDU reactor there. He then took a position looking after all of the systems for retubing the reactors. Basically process engineering to remove and inspect the reactor components.
What does a retubing look like from start to finish?
(25:48) The first step is to install tool control system platforms all around the reactor, these hold up the programmable logic controllers. Sometimes Robert would install cranes or temporary doorways in the building to get the tools in and out. Then each platform would have an automated worktable installed, each of which would perform different functions. All of the systems are controlled by a human technician but from farther away from the reactor in the control room. They control the robotic systems located inside the reactors.
How many days does refurbishment take?
(36:20) It depends on the reactor, but several months, 18 to 24 according to Robert. And once the retubing team is finished with replacing the fuel channels and all of the components are back together, and the tooling system has been removed, that is when the reactor systems get recommissioned. That process can take anywhere between three and nine months.
If we build a lot of new nuclear reactors, they’ll likely all need to be refurbished around the same time in 25 years. Where will we get the energy from during that period of time?
(38:26) In Ontario, one unit was built at a time. And now, that’s the same way they’re being refurbished. For example, at Darlington they’re refurbishing each unit separately to avoid having to shut down all four at one time.
Future of Nuclear Refurbishment
(47:14-54:45) Robert gives his take on the future of nuclear.
It’s important to have a mixture of different types of engineers working on these projects, how do you see the future of nuclear changing?
(47:14) Robert has seen a lot of computer programmers coming to the nuclear field and he thinks there’s going to be an increased need for that skillset. But the world of automation and logic control programming is expanding.
What is the main purpose of retubing?
(48:43) Overtime, the pressure tubes in the reactor grow, sag, and elongate with irradiation. They were only designed to grow a certain amount before they no longer remain on the bearings of the fuel channel.
How is the growth measured?
(49:34) As part of inspection programs, measurements are taken by the refueling machines to measure length.
Now, in your career, are you still very hands on during these processes or do you play more of a managerial role?
(50:18) Robert does a bit of both, he leads the retubing and inspection staff, but he also works to continue developing and supporting systems in the field. He contributes to the design review process. He also goes down to the laboratory at least once a day to check in on things that are developing. Robert’s staff numbers about 215 and more than half are in the lab; the other half are in the field. He currently has about 30 projects ongoing in the lab. They could be large refurbishment projects or smaller inspection contracts. His team works on a lot of inspection tooling.
After decades in this field, do you support nuclear?
(53:20) From day one Robert supported the nuclear industry and wanted to be part of it ever since he went on to get his master’s degree. He wanted to understand the problems the nuclear industry was facing. Robert hopes the nuclear field grows and public understanding of the technology increases, especially how green it is.
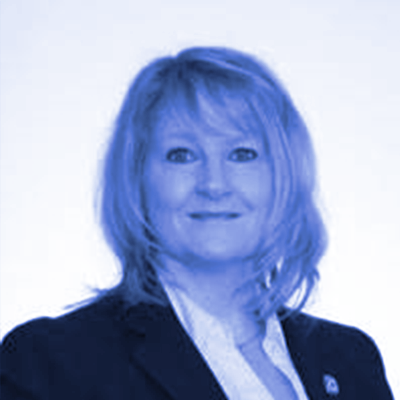
1) SNC Lavalin's role in developing CANDU reactors and designing for advanced fuels
2) SNCs strategy for bulding 1 CANDU reactor for every 4 PWRs
3) How SNC Lavalin designs, develops and tracks their product development and performance
4) Leveraging SNC's experience in licensing approval
1) How did you get into the nuclear field? 1:43
Catherine Cottrell is the Senior Director of Product Development in the nuclear sector. About 60
percent of total power generated in Ontario comes from nuclear energy. Catherine got her
degree in chemical engineering and has been with SNC-Lavalin for 22 years.
Catherine says that chemical engineering principles are applicable to the nuclear field,
especially knowledge in process systems. She’s constantly learning at SNC-Lavalin from her
colleagues in all of the different offices.
Her first role at SNC-Lavalin was in isotope production as a process engineer. Catherine worked
to design the facility to extract the isotopes and make medical isotopes used in diagnostic
medicine.
Catherine got into nuclear when looking at CANDU fuel cycles.
CANDU stands for Canada Deuterium Uranium. This type of rector is unique in that it can use
natural uranium, whereas other reactors use enriched uranium. To make the rector run, CANDU
reactors use heavy water. Natural uranium is plentiful in Canada, which drives the use of natural
uranium.
SNC-Lavalin has a mining office, but they act as a designer or vendor, but do not own or run
any rectors. SNC-Lavalin sells their designs to nuclear facilities and is the original equipment
manufacturers.
CANDU reactors are unique in that they can use spent fuels from other rector types to generate
power. Her first job was to work with international colleagues from the two CANDU reactors in
China. The Chinese clients were trying to find a way to use other natural resources in their
plants, since China does not have a lot of natural uranium resources. Since China has a lot of
pressurized water reactors (PWR), they are now able to take the spent fuel from those reactors
and use it in the CANDU reactors. Therefore, CANDU reactors recycle spent fuel from other
rectors and obtain more energy.
2) What is the process of fuel storage? 8:53
The uranium fuel bundles, which are about half a meter long, go into the rector and then the fuel
bundles come out of the rector in the same way. The bundles are then safely stored in a spent
fuel pool to cool and decay. The spent bundles are then transferred into a storage container on
site to be monitored and controlled. SNC-Lavalin designed and built the safe storage containers.
3) If we start building more heavy water reactors and less pressurized water reactors, will
we still need to invest in recycling the waste from pressurize rectors? 9:49
Ideally, Catherine would love to focus more on heavy water reactors. But something else that
can be done with a CANDU reactor is to use thorium. Thorium occurs naturally in the Earth in
two or three times greater amounts than uranium. CANDU reactors are the best type of reactor
to utilize thorium, according to Catherine.
Catherine believes all types of reactors are important, but working together with all of the
different types of reactors allows the nuclear field to close the fuel cycle.
4) You work mainly on the fuel cycle and looking at different types of fuels? 10:50
Catherine’s previous work was successful in demonstrating that CANDU reactors can process
different types of fuels. That work was used in the development of a new reactor. That reactor
would be designed to utilize even more of the fuel and improve efficiency and get extra burn up.
This type of reactor could use advanced fuel cycle or either recycled spent fuel or thorium fuels.
Depending on the type of fuel selected, Catherine would work to test the physical properties in a
research reactor, like Chalk River Laboratories. Working with a lab Catherine is able to conduct
controlled testing, collect data, and verify and validate the design process.
5) Since 60 percent of Ontario’s energy comes from nuclear, the Canadian government
seems highly invested in nuclear power? 13:55
Absolutely, says Catherine. In Ontario two nuclear plants are undergoing reactor life extension
projects called refurbishment. The government is invested and has put forth funding to make
sure that the reactors continue to run.
In Canada there is an ongoing project by the Nuclear Waste Management Organization to
locate a deep geological repository for spent fuel. The organization is going into communities to
gauge interest and will be selecting a site in the future. Catherine says many of the communities
are embracing and welcoming the repository project.
Catherine says that much of the spent fuel from CANDU reactors has a low level of enrichment
since it came from natural sources. So it is probably unlikely that this type of fuel can be
recycled, unlike the spent fuel from other types of reactors.
6) Why doesn’t Canada have pressurized water reactors? 16:08
Canada doesn’t have PWRs; instead Canada has CANDU reactors, which Catherine says are
the best. The model SNC-Lavalin is working towards building CANDU reactors in countries
without high levels of natural uranium, or places with other types of reactors. This way, new
CANDU reactors can recycle spent fuel or process thorium. The goal is to build one CANDU for
every four PWRs. SNC-Lavalin is primarily focused on working with China to bring this
technology to China because there is such a large fleet of PWRs.
7) How do you market nuclear as a product? 17:38
According to Catherine, CANDU technology is one of the best performing technologies in the
world. SNC-Lavalin has been working on this type of technology for many years, whereas other
nuclear vendors have not spent as much time invested in developing CANDU. Catherine thinks
the perceptions of nuclear can be improved by continuing to demonstrate the safety of CANDU
reactors, and by providing clean energy from a nuclear reactor, and safely storing spent fuel
until the end of its life. Catherine thinks that the nuclear industry can be more forthcoming about
what their technology can do and the benefits nuclear power brings. Promoting the facts is
important, she says.
CANDU reactors can also produce isotopes, which is important for the food industry and
pharmaceutical industry. These particular isotopes provide sterilization.
8) What’s the most exciting project you’ve gotten to work on? 20:30
Catherine says the most exciting project she’s ever worked on was the fuel cycle project. It was
the first time they’ve put a new type of fuel into a reactor and been able to demonstrate that it
behaved as expected. SNC-Lavalin tested this process in the CANDU reactors in China.
The entire project took about three to five years. Catherine says there were challenges, but that
their team and their partners in China embraced any complications and worked together to
solve them. The Chinese have since approved the use of the advanced fuel on CANDU reactors
and full scale will be implemented soon.
9) What’s next for you? 21:47
As Senior Director of Product Development Catherine will now overlook all of the products that
SNC-Lavalin produces. Some of the up and coming products include a cable tester that can be
used to test the health of electrical cables in reactors without having to shut them down. Cables
have to be tested every two or three years, so this improved version makes it easier and less of
a hassle to do routine checks. This cable tester has evolved over the years and SNC-Lavalin’s
new cable tester can measure the recovery time, which is a better indicator of the aging in some
types of cables.
Catherine keeps a close eye on markets to monitor if technology is still relevant and if not, how
her team can modify it through feedback from customers. Catherine’s team has approximately
20 products under development. Right now SNC-Lavalin is heavily investing in designing retube
and refurbishment tools.
10) Can you describe more of your work with CANDU reactors? 29:57
Catherine says a lot of preparation and training goes into refurbishment projects. Her team is
working to design and produce improved retubing and refurbishment tools to make the process
faster.
Her team also works on the new build or an advanced CANDU reactor. Catherine says there
are three types of reactors: the CANDU-6; the advanced fuel CANDU reactor, which is an
upcoming release; and the enhanced CANDU-6, a generation three reactor, which is available
for sale. The latter two have post-Fukushima improvements to enhance safety.
Being in the nuclear field, Catherine has learned a lot from interacting with various members of
the SNC-Lavalin team. She thinks that nuclear has to play a large part in the future of power; it
provides the base load of energy. Ultimately, she believes we should have a mixture of other
types of energy, specifically renewable. Catherine hopes that people can learn that nuclear
power is safe and it provides clean energy.
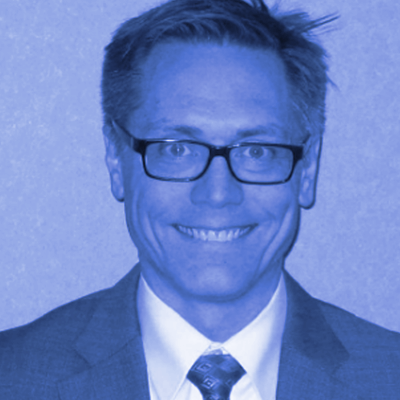
1) How growing up in Sweden shaped christers views on nuclear and eventual path to becoming a nuclear power plant operator the principal engineer at GE-Hitachi
2) Designing nuclear power plants with licensing in mind to address prelicensing and site specific licensing technicalities
3) Simplifying system level changes in a nuclear power plants
4) The MWRX300 small modular reactor and it's path to the commercial market in 2030
Sweden’s position on nuclear (0:09)
0:09-7:53 (Christer discusses Sweden’s position on nuclear power and how he became pro-nuclear from an anti-nuclear upbringing.)
Q. You grew up in Sweden? What was that like?
A. Christer Dahlgren is the Principal Engineer for GE’s BWRX300 project. He grew up in a town near Stockholm. During that time, Sweden gained over half of their power from nuclear energy. But after Chernobyl, attitudes towards nuclear changed in Sweden, including Christer’s parents who held an anti-nuclear position. Since Chernobyl, attitudes are beginning to change again. Sweden has achieved carbon free electricity and has used nuclear energy to power industry. While Sweden has developed their wind power, it does not generate enough power alone. Additionally, Sweden has expanded their hydropower as much as possible. If Sweden is unable to continue exporting clean power, neighboring countries will turn to rely on Poland or Germany’s coal power. Changing Sweden’s general views on nuclear power requires overcoming stigma. For Christer, this happened through research. He learned that, compared to other fuels, nuclear is extremely safe. It also takes little space and leaves little waste. Nuclear power also causes the economies of local communities to flourish due to the good pay and high employment.
Learning how to operate a nuclear reactor (7:54)
7:54-18:37 (Christer explains the new GE reactor design and how he transitioned from analytical work to nuclear power plant operations.)
Q. One of the things you’re looking at with the new BWRX300 design is reducing the number of people it takes to operate the plant, right?
A. Yes. Staffing a nuclear power plant is a high cost. The new BWRX300 will still require people to operate the plant, but will have less people and more centralized support than larger models. Smaller models will not reduce the number of nuclear employees overall. For instance, a large plant could staff 800 people while 20 small plants could staff 80 people each for a total of 1600 employees. Because smaller plants cost less and take up less space, more plants can be built than large models.
Christer first became interested in the nuclear industry after taking energy classes in college which sparked his interest in power production. He was then offered a place in the nuclear program at Sweden’s Royal Institute of Technology. Christer focused his master’s thesis on a small reactor that had existed in the center of Sweden. This reactor provided heat during the 1960s and 1970s, but was subjected to a major flooding event. Christer conducted thermohydraulic analysis of the plant and explored the consequences of the accident.
This type of reactor generates district heating which provides heat to a city. Christer sees district heating as an easier way to increase the number of nuclear reactors around the world because much of the current district heating is powered by coal. This is a great entry point for a light water reactor (LWR), which could be used to replace the coal power facilities. However, siting must first be explored to understand which cities can build an LWR. Some countries are not adapted for small reactors but instead only focus on large reactors. The US, on the other hand, may be shifting towards accepting more small modular reactors (SMRs) because the NRC has just proposed a change to the emergency protected zone (EPZ) regulations, which create a minimum boundary around a reactor to protect against accidents. SMRs can have smaller boundaries because they are smaller reactors, and the NRC is beginning to change regulations to reflect this.
After studying the district heating reactor in Sweden, Christer moved to the US and worked with an RBMK reactor, which is the same reactor design as Chernobyl, in Maryland. Christer decided to stay in the US to pursue a PhD at the University of Maryland in College Park. Here he simulated the loss of coolant accident. Christer then began wondering about the actual operations of a nuclear facility, and moved to Michigan to work at the Palisades power plant. He learned a great deal as a reactor operator, stating that he was able to learn something new everyday for 6 years. Coming from an analytical background, this opportunity taught Christer how take a more hands on approach to nuclear power, learning how to respond to events.
Licensing strategy for the BWRX300 (18:37)
18:37-26:54 (Christer gives an example of a nuclear event that he learned about as an operator. He also explains why he began working at GE and introduces the licensing strategy for the new BWRX300 design.)
Q. How do nuclear reactors respond to a transient?
A. The pressurizer within a nuclear reactor can maintain pressure in most transient (a change in the reactor coolant system involving temperature and/or pressure) cases. Several types of events can cause a transient. A pressurizer will not maintain pressure when there is a break in a pipe that causes a leak. It can, however, maintain pressure during a power loss. Transients are caused by either an operator action, such as an intentional cool down, or if, for example, a valve were to fail and open unexpectedly.
After 6 years, Christer grew bored of plant operations and moved to GE where he works on plant designs. He is currently working on the new BWRX300 design. Part of this process is anticipating the licensing process that GE will eventually go through. This includes communicating key issues early on with the NRC to review initial concerns, which will reduce licensing risks later on. To avoid prior problems of spending millions of dollars on licensing fees only for a design not to be built, GE is focusing this time on site specific licensing. This means that they make generic site assumptions to find the most optimum approach.
Optimizing the BWRX300 design (26:55)
26:55-34:46 (Christer discusses the overall approach to designing the BWRX300. )
Q. What was the overall strategy for BWRX300 and how does one design a plant from ideation through to it actually being built?
A. The BWRX300 design began with eliminating the coolant loss accident by simplifying systems. This change resulted in the possibility for a smaller plant design. The strategy was to keep the core systems at the highest safety class and fit them into the most optimum structure possible. This results in a design which is twice as cheap due to the decreased about of concrete required to build the plant. Concrete costs dominate overall project costs, pushing the design team to limit the amount of concrete in the design without sacrificing safety. This required a breakdown of the preconceived notions around what a nuclear plant looks like. This lead to moving the design of the plant underground, which also protects the plant from external hazards. They are also looking into the structures that could be moved outside of the plant to optimize the design further. Additionally, boiling water reactors (BWRs) run at a lower pressure than pressurized water reactors (PWRs), meaning less concrete does not create pressure issues that may be present in PWRs. The BWRX300 design also utilizes metal and has removed the pumping systems. The reactor will be built in a factory and shipped to the site, meaning the design will be further optimized to ensure it can be shipped over roads and assembled on site.
Justifying BWRs over PWRs (34:47)
34:47-43:45 (Christer notes the reason for forging, instead of welding, a pressure vessel. He also discusses his support in designing a BWR instead of a PWR.)
Q. Has anyone pushed back on the requirement to have a forged (single piece) pressure vessel?
A. The configuration of a reactor vessel drives whether or not it is forged. Welds require further inspections, so to save on operation and maintenance (O&M) costs, GE prefers forging. Christer has studied welds from old reactors to determine the effect of neutron bombardment and notes that there is an effect when welding using copper and nickel material. The size of the vessel can also not be reduced greatly because there must be space inside the vessel for the converted steam in a boiling water reactor (BWR). However, they are still smaller than PWRs and can be forged easily in one piece. Additionally, welding creates more complications, and Christer is focusing on simplicity for the BWRX300l.
Even if Christer did not work at GE, he would still choose a BWR over a PWR. This is because the new design must be cheaper and inspections of PWRs are more costly. BWRs and PWRs operate similarly in terms of performance, but the BWRX300 has a more simple design than PWRs. Christer notes that cost can make or break a project, and so optimization is key to the design’s success. Christer’s team is still working on the logistics of optimizing the serviceability of the design, but notes the inclusion of equipment hatches to ensure maintenance can be carried out. Additionally, the fuel building is inside the reactor at the top of the reactor vessel, so there is no transfer of fuel. While the lifetime of the design is shorter than PWRs, the lower cost justifies this because investors will receive a return much sooner.
Designing plants differently (43:46)
43:46-48:51 (Christer discusses the ways he has pushed to do things differently in the nuclear design process.)
Q. How do you find it to be when pushing to do things differently than the way they have been done before?
A. Christer works with experts in the nuclear industry. His colleagues have the historical knowledge of designs that have and have not worked. Christer therefore knows if the new ideas will work or not. For instance, Christer is confident when discussing the decision to use natural circulation instead of pumps. Pumps change the pump flow rate which decreases or increases power output. However, the BWRX300 is based on the previous BSWR design, which does not include pumps and has already undergone the expensive licensing process. It is therefore much cheaper for the BWRX300 design to rely on natural circulation.
Additionally, Christer is changing safety classifications. He looks closely at the International Atomic Energy Agency (IAEA) regulations involving defense lines. Defense lines state that a nuclear plant must have multiple safety systems. Christer optimizes safety by overlaying plant functions and running probabilistic risk analyses. He uses this data to identify redundant safety features and aims to create a framework that creates a rigorous defense line architecture for all systems. This creates a new, transparent decision making process for safety systems and safety classifications.
Approaching different countries for safety approval (48:52)
48:52-54:15 (Christer explains the need for safety systems and the differences between various country’s nuclear regulatory systems.)
Q. Your plant is underground, so how could any radionuclides escape from underground in the case of a meltdown?
A. The design is essentially a cylinder with a pool on top. We do, however, need additional safety systems. These include SCRAM (emergency shutdown), isolation and heat exchange. Additionally, systems must have backup functions and there must be 3 tiers of safety systems.
Although this new safety system has been approved by both Finland and the UK, GE has yet to talk with the NRC. Both Finland and the UK have a tough but pragmatic nuclear culture. Finland requires a great deal of information before approving a project. The UK prefers to engage in dialogue. Canada is IAEA-centric and has rational safety classifications based on where a function is applied. The IAEA has a good framework, allowing GE to adapt to be country-specific.
Christer’s timeline for saving the world (54:16)
54:16-1:02:29 (Christer explains why the BWRX300 will not be built in the next 2 years. He also explains the importance of nuclear energy for the future of humanity.)
Q. What is your timeline for saving the world?
A. The first BWRX300 is expected to be built by 2030. Meeting this goal depends on both GE performance and the willingness of the customer to help, such as by finding a site. Speeding up the design process to build a plant in 2 years relies on a firm commitment from the customer, identifying a site and conducting investigations. However, licensing slows the design process down. Even in countries that do not have existing nuclear regulations, GE must wait for the country to establish one, which is not a fast process. This means that we must wait more than 2 years for the first BWRX300 to be constructed.
In Christer’s mind, nuclear power is important for the future of humanity because decarbonization can not be achieved through renewables alone. Nuclear energy can achieve a decarbonized electric system and district heating on a major scale. Further, nuclear is critical to stopping and reversing climate change. As the number of customers enable more small, cheap plants to be built, costs will decrease and more countries will be able to finance and implement nuclear projects. Christer’s overall goal for nuclear is to create a low cost power that will not rely on government subsidies.
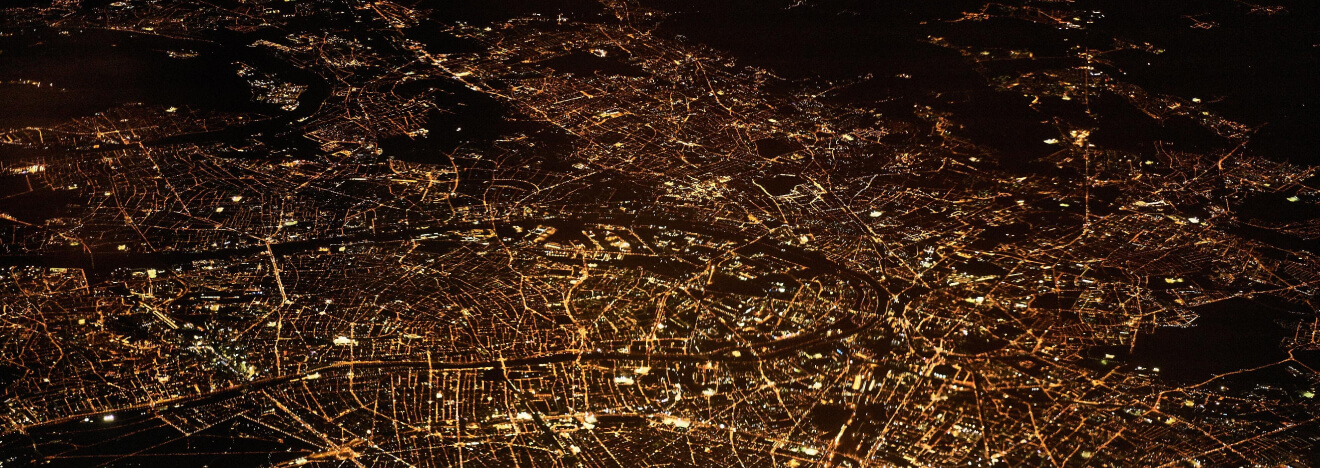
Sign up for our newsletter
No results found
Please try different keywords