Ep 190: Robert Plana - Chief Technology Officer, Assystem
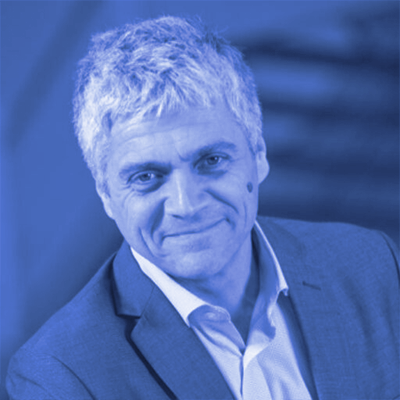
Show notes
Developing a career in problem solving (0:38)
0:38-9:02 (Robert discusses his background and how he developed a mindset that he finds useful when working in the nuclear sector.)
Q. Can you tell me about your background, where you grew up and how you got into the nuclear space?
A. Dr. Robert Plana comes from the South of France where he received a PhD in Information and Communication Technologies. He initially was more interested in sports but quickly was drawn to research because Robert loved that he was able to discover new things. It is here where he developed a mindset that he found useful later in the nuclear industry. This mindset focuses around never giving up and finding alternative routes when you refuse to do something. This is applicable to the nuclear sector because projects are huge, there are many interfaces and the process is long.
Robert has a rich background, studying such things as physics, electronics and electromagnetism. His first research career was in the Internet of Things (IoT) domain in the early 2000s. No matter the subject, he is driven by the scientific and innovation aspects that come with a career in problem solving. This interest probably stems from Robert’s father, who was a physics professor. Robert did not pursue a career in teaching because he was bored by the lack of innovation opportunities. Robert is now the Chief Technical Officer (CTO) of Assystem.
Determining innovation investments (9:03)
9:03-16:02 (Robert discusses how his role as CTO enables constant innovation. He also explains the different readiness level scales [TRL and BRL] and how these are used to fund Assystem’s innovation projects.)
Q. Your role now is probably different from teaching, where you are now looking at a lot of new ideas and innovations, right?
A. Yes. Robert is constantly looking at new ideas. His primary role is to detect talent and new ideas within Assystem and make sure these are leveraged to elevate the business. Robert defines innovation as the process of transforming an idea into a business opportunity. Robert creates an innovation roadmap to help direct investment within Assystem. He uses NASA’s Technology Readiness Level (TRL) scale to determine the stage of innovation a project is in. Projects that fall between 1 and 3 are in the research phase, those between 3 and 6 are demonstrators and those in the 6 to 9 range are ready for product development. Robert has developed the Business Readiness Level (BRL) scale which he uses to help determine which products to produce. In the BRL scale, projects between 1 and 3 have no existing business case, those in the 3 to 5 range have some existing business case but the market is not yet well defined and those falling between 6 and 9 have a market that is ready for the product. Because Assystem must balance risk, about 75% of funded projects fall in the BRL 6 to 9 range to generate business revenue. A small percentage of funded projects fall in the 1 to 3 range because although they are risky, Assystem must invest in the anticipated future.
Improving efficiency with Artificial Intelligence (16:02)
16:02-28:15 (Robert describes what projects are currently in the BRL 6-9 range. He also explains how Assystem is using AI to improve efficiency of project design.)
Q. What projects are in the BRL 6-9 currently?
A. One project in the BRL 6 to 9 range is a project to develop additional bid services which will enable Assystem to introduce new functionalities such as class detection and cost estimation.
Another project involves accessing the amount of data present in the nuclear industry. Electronic data enables data manipulation which can lead to new service opportunities. Currently though, there is a wealth of historical nuclear data in paper documents. Documents are often written and read by multiple people, which can lead to misinterpretation of information when analyzing information. These errors can affect the physical architecture of nuclear facilities. To get around this, Assystem is using Artificial Intelligence (AI) to automatically extract data from documents. This eliminates human misinterpretation so the proper functional, logical and physical architecture data in design reports are captured in a more robust way. The data in inspection reports can be used to generate hot mapping, which creates clusters of sensitive and critical areas based on malfunction data, for example. This enables Assystem to focus and optimize maintenance and prevent problems from occurring in future designs. Assystem has 50 years of nuclear data which can be leveraged to create more efficient projects moving forwards.
Data driven approaches decrease costs (28:16)
28:16-32:41 (Robert describes how a data driven approach reduced a project’s cost by 30-40%. Robert also speaks about the need to attract a wider range of engineers and data managers to Assystem.)
Q. What are some of the biggest flaws that Assystem has extracted from old data which has turned out to be a huge cost or time saver?
A. Assystem is working on a waste management project. The team used a data driven approach to create a digital twin of an existing facility. Digital tools were also used in the testing and commissioning phase. This approach saved Assystem 20% during the design phase and between 10 and 20% in operations, creating a total cost savings of 30-40%.
Not only does this type of innovative approach save Assystem money, but it also saves their limited human resources. Assystem does not have enough engineers and needs to attract mechanical, electrical and ventilation engineers as well as data managers and system engineers.
Some exciting Assystem projects (32:42)
32:42-38:51 (Robert describes three interesting projects that he has worked on as Assystem’s CTO: SMRs, hot cells and machine vision.)
Q. What are some of the most interesting projects that you’ve worked on as Assystem’s CTO?
A. Robert has worked on Assystem’s small modular reactor (SMR) project. New modular designs can accelerate both the design and construction phases. SMRs are built in factories and then assembled at the new nuclear site. Assystem is co-developing SMRs with Rolls-Royce in the UK.
Robert also works on the hot cell project. A hot cell is essentially a containment box to increase radiation safety. They range in size and Assystem is designing a large hot cell for ITER, a major international fusion reactor project.
Another safety-focused project is the development of Assystem’s machine vision. This aims to advance inspection of nuclear facilities, such as the UK’s graphite reactor. Due to radiation levels, reactor inspections can be impossible because microscopes are needed to identify and monitor very small cracks that may appear in a reactor. An advanced camera, a laser system and sophisticated data processing is used to detect cracks on the 50 micron scale. For reference, one micron is the diameter of a single human hair. It is important to detect cracks as soon as possible to understand what caused them and to monitor them as they grow in size. Radiation, stress and incorrect designs can lead to cracks and reactors must be stopped once a crack reaches a prespecified size. Machine vision, modeling and AI can be used together to understand the physics of reactor cracks.
Crack monitoring with machine vision (38:52)
38:52-46:04 (Robert expands on the machine vision project, focusing on the safety and financial reasons that support crack monitoring.)
Q. Is crack monitoring more important in nuclear because replacing a facility is more costly than, say, a water treatment plant?
A. It is primarily a safety issue. The reasons for cracks and how fast they will grow is unknown, so using machine vision to monitor cracks is a zero risk approach. Graphite, for instance, is a complex material and the physics of its surface energy is not well understood, meaning interactions are not well known. This is another reason for close monitoring of cracks, which is crucial because safety authorities will shut down reactors once a crack reaches a couple of centimeters.
Recovering from a crack will take many months because a reactor must be shut down in order to be fixed. It must then go through the commissioning phase again before it can regain operation. Machine vision therefore saves time and money.
Today, Assystem’s machine vision model is in its first demonstration and resolution is still improving. Robert explains that a few more years of research and development (R&D) is needed to incorporate more data and expert knowledge to run further simulations. While the project is very complicated, it is also exciting because the knowledge learned in this project can be applied and reused in other domains.
Predicting nuclear facility maintenance (46:05)
46:05-55:46 (Robert describes the predicted maintenance project and how it will be used to decrease costs while increasing optimization.)
Q. What is predicted maintenance?
A. Predicted maintenance is a model that predicts the lifetime of a system. It enables operators to know when to perform preventative maintenance to prevent machine failures. The current nuclear facility maintenance schedules ignore the Health Index of an asset. This is when, for example, a car that is driven in a snowy climate ages differently from one that is driven in a different climate. Assystem uses data and sensors to create the Health Index of the machine to understand how nuclear machines age under different operating conditions. This is then used to calculate the Mean Time to Failure and identify key performance indicators (KPIs). This will allow operators to understand a nuclear plant’s lifetime and schedule maintenance according to when it is needed. Optimization plans can also be proposed to increase a machine’s lifetime. Predicted maintenance has been implemented in the oil and gas industry, decreasing maintenance costs by 20%. It should therefore also be implemented for nuclear to decrease costs.
Assystem’s first predictive maintenance project involves screen cleaners, which are the screens that stop debrey, such as trees, from entering a nuclear reactor’s cooling system from the nearby sea or river. If a screen cleaner malfunctions, it could restrict water from entering the cooling system, raising the temperature of the plant and resulting in plant closure. Assystem’s predictive maintenance model for the screen cleaners monitor data every day which are used to generate reports that are sent to the operator. The model is refined if defects are detected and the Mean Time to Failure is calculated. Assystem can then design and propose the maintenance inspection schedule for the lifetime of the screen cleaners. External data, such as tide levels, weather conditions and the season, are used in the model. Assystem will eventually move towards ending reliance on physical sensors and instead use virtual sensors in the coming years.
Accelerating projects and improving safety with technology (55:47)
55:47-1:01:37 (Robert explains the dismantling project and his vision for the future of a technology-enhanced nuclear industry.)
Q. Tell me about the last project you’re working on?
A. Dismantling is the other project Assystem is working on. CEA, a nuclear reactor R&D organization, has access to 14 million physical documents. Assystem has created an AI algorithm and search engine to automatically read these documents and answer questions. This technology will enable better team organization and will minimize hazards during the dismantling process through automated infrastructure mapping and information organization.
Moving forwards, Robert sees the nuclear industry advancing system engineering. He foresees a critical role for modeling, data and AI in accelerating the way the nuclear industry designs, commissions and operates in the future. Robert also believes in the development of modular reactors as it is another way to accelerate design and construction. Predicted maintenance will also optimize processes while increasing safety and maximizing efficiency.
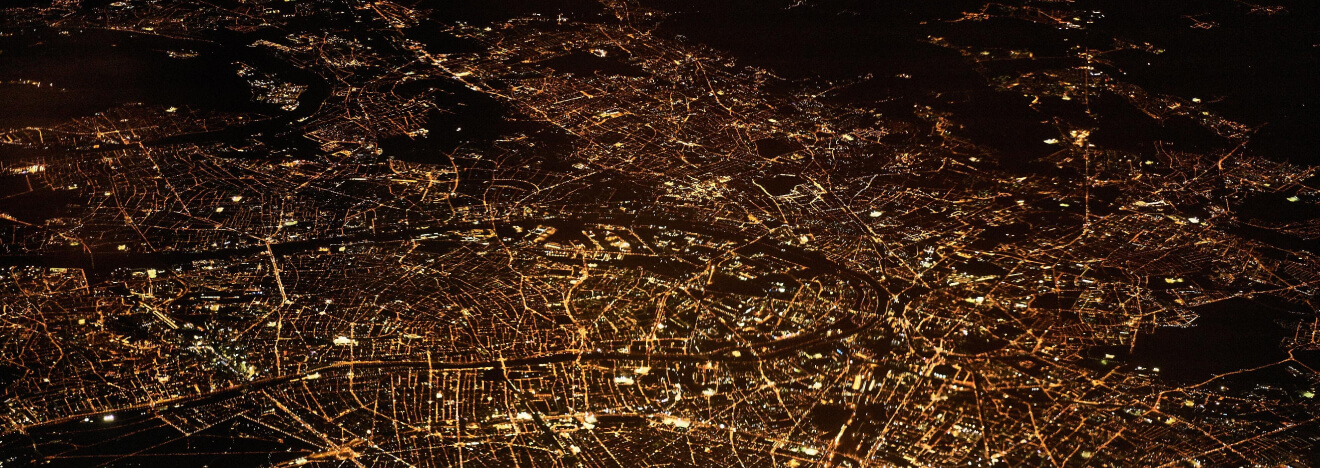