Ep 271: Rich Deakin - Director, Low Cost Nuclear Challenge, UKRI
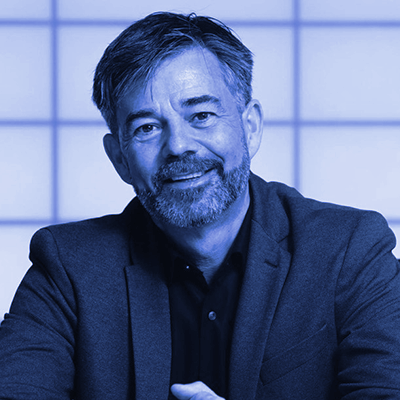
Show notes
From Metallurgy to Manufacturing (0:00-14:38)
(Rich Deakins looks back on how his education in metallurgy led him into operations management in nuclear fuel manufacturing)
Q: How did you learn about nuclear energy?
A: Rich Deakins grew up in the coalfields of northern UK, around the heavy industry areas of South Yorkshire and Sheffield. Both his father and brother were underground coal miners. During his late teenage years, UK experienced an industrial shift around the economics of coal, threatening the industry. Rich went on to study metallurgy at Sheffield University. The four-year degree program included two six-month work experience placements. Rich ended up working at the UK Atomic Energy Authority where he did research on void swelling on nuclear radiation damage in stainless steel. Brittleness, dimension, and shape of a metal can all be changed by radiation. When a metal is put in front of a radiation source, damage is done to one side caused by neutrons knocking atoms out of the lattice and coming together to form a gas bubble. During his early years i/n university, Rich started planning strategically one year ahead, not knowing what he wanted to do long term. Young grads shouldn’t look too far ahead, but show up and know what you want to get out of it. Rich’s second placement during university was at one of the big generating boards, a UK utility, which was a nationalized industry at the time. His work was focused on completing insurance claims and analyzing machine failures on power stations. Rich got exposed to nuclear and hydro power stations during this time. During his time in school, Rich identified areas of study that he wasn’t very comfortable with and focused on learning those subjects thoroughly, eventually leading him to receive a first class honours degree. He received an offer after graduation in the technical department at Springfields, the home of UK’s nuclear fuel fabrication since 1960. All the magnox fuel in the UK and all the oxide fuel for the advanced gas reactors (AGR) was made at Springfields. Rich worked around icons of the industry, who encouraged him to explore the operations side. He got a position on the operations management team as an assistant plant manager on one of the main line oxide fuel plants. Rich was responsible for the blend recipes for AGR main line enrichment blends. Most enriched oxide plants are either limited moderation, safe by shape, safe by mass, safe by moderation, or they have burnable poisons. At that time, the AGR fleet was ten or eleven reactors, all slightly different and all operating on slightly different enrichment levels and fuels. Production starts with a powder, goes into granules, pellets, fuel rods, fuel bundles, and to the station. Progressively, these steps get more complicated as the process advances, especially with 20 or 30 fuel variants.
Innovation in Nuclear Fuel Production (14:38-31:54)
(A look at how Rich brought success to some of nuclear fuel manufacturing’s biggest operations challenges in the UK)
Q: I never thought that the fuel could be different, driving up fuel costs, operations costs, and overall the cost of power more expensive.
A: In his late twenties, Rich Deakin was working as an assistant plant manager on one of the main line oxide fuel plants at Springfields. The fuel division of British Nuclear Fuels called the Springfields site, realizing that a change was coming in terms of customers because the UK electricity market was about to be broken into the North and South boards and eventually be deregulated. Nuclear fuel had to be thirty percent cheaper to survive in that market. British Nuclear Fuels tried to kickstart a just-in-time manufacturing program aimed at finding the right balance between keeping the workforce busy and producing the right products. This strategy focuses on supply chain management, value stream mapping, and constraint theory which identifies the bottlenecks. Three assistant plant managers, including Rich, were promoted to plant manager in order to try running things differently. Rich had to get very good at actually fixing problems that were previously bearable. Without inventory or stockpiles to go to, breakdowns are fixed when things more quickly. Productivity was improved by 25% over three years. The lead time for fuel went from two-and-a-half years to a maximum of six months. This led the company to question whether twenty-odd variants of fuel were actually needed and if the marginal difference in performance was worth the extra cost to manufacture. Rich reduced the number of fuel types down to six or seven variants. This also helped reduce the amount of material that needed to be stockpiled. Nuclear has progressively looked at technical gain in the reactor systems, rather than the overall cost of delivering power. Rich was asked to go to Sellafield to make mixed oxide (MOX) nuclear fuel. Sellafield has been the center of reprocessing and waste storage in the UK. It was also the site of the first commercial power station, Calder Hall, a Magnox station in 1958. Four reactors were built and put online in three-and-a-half years. Sellafield was a reprocessing facility generating plutonium oxide. The question is whether the activity still latent in that material is a liability or an asset. One mechanism for closing the cycle was to blend it with uranium and put it back in fuel assemblies sent to reactors. This was done at the Sellafield MOX Plant. The plant wasn’t particularly easy to operate and was challenging to commission, mostly because of the way the components were connected in the system. Rich was appointed head of manufacturing in that facility and asked to get it to go with his team. When Rich picked up the business, he decided his team needed to get away from planning and feel successful by solving a problem in the plant. The speed at which you commission is determined by a simple cycle: how fast you can identify where the problem is, usually based on the data collection system; how fast your people can understand it and identify the issue; how fast your team can find a potential solution; and, how fast your team and can trial and error to put it in place. In nuclear, the trial and error phase gets tricky because of change management plans and risk assessment. Rich advocated that the ownership of an issue should belong to the individuals that can fix it. Managers and leaders own the responsibility to give the team space to do their work. Rich took the plant from zero to four fuel assemblies, right the first time with the certification date approaching half a million data points, all concession free, in 18 months. The key is good data and ability to find the problem and implement solutions.
The UK Government’s Investment in Nuclear (31:54-47:52)
(Why the UK is pursuing small modular reactor technology and how manufacturing methods can impact the success of the industry)
Q: What role are you at now and what are the challenges you are trying to take on?
A: Rich Deakins was an operations-making type, as opposed to reprocessing or project management. After Sellafield, it was not obvious what his next move would be, so he left to get some international experience in a different sector. Rich was asked to be a general manager head of manufacturing for a Rolls Royce Aerospace site. His job was to transition an old site to a new site within the aerospace network. Rich learned a lot in this role, such as dispersed supply chains and external supply chain management, but both the aerospace and nuclear industries had a similar focus on quality. Rolls Royce has a division which designs, builds, and services nuclear reactor cores for the UK Navy. Rich was offered the role of general manager and agent of the site licensee, making him accountable for running a nuclear licensed site, where he worked for five years. After his five years in Rolls, Rich went to work for NuScale Power in Oregon as the program director for their first-of-a-kind engineering and validation effort. He returned to the UK and joined the UK government as a policy advisor within the Department of Business, Energy, and Industrial Strategy (BEIS) advising UK government ministers on what’s needed to bring forward the commercialization of small nuclear power in the UK. In 2014, the UK hosted a small modular reactor (SMR) competition to try and downselect what small nuclear technology offered the best value for money as a proposition for investment by the UK. It actually compared small nuclear on a like-for-like basis with large generation programs, determining it doesn’t work based on economies of scale if all things are equal. There is a different risk profile than delivering something that is factory-built in a controlled environment than something that is field-built as a project. Small nuclear looks at developing a product, not a project. In 2018, BEIS commissioned the Expert Finance Working Group which took six or seven independent experts from the City of London to see if commercial finance could be attracted to small nuclear programs. One theme that emerged was the financial community didn’t understand the risk profile of nuclear, particularly small nuclear. When Ford built the first Model T in Michigan in 1908, it wasn’t about the internal combustion engine - it was about the method of factory-built manufacturing. This is what needs to be done with small nuclear. There will be step changes and technology evolution along the way to fit in different applications and markets, but they will all be built the same way. Rich decided he wanted to explore the development of UK SMR technology. In July 2019, the UK government decided they would cofund the first phase of a UK SMR program and committed to a series of programs run by UK Research & Innovation designed to enable developments and deliveries of significant projects that might impact societal growth. Rich left the government and is now the UK Challenge Program Director for the Low-Cost Nuclear Challenge. The mission is to de-risk the research and development of a small nuclear delivery model to the point at which commercial and private financers can be attracted to it at competitive rates.
Low-Cost Nuclear Challenge (47:52-1:01:47)
(Rich explains how the combination of government and private investments has decreased nationwide emissions and fed into the nuclear supply chain)
Q: Are private nuclear developers applying for the money through the Low-Cost Nuclear Challenge?
A: Rich Deakins is the Challenge Program Director for the Low-Cost Nuclear Challenge in the UK. Rolls-Royce, with a consortium of partners, came forward and bid into the industrial strategy fund. They believed they had a program which could attract a private developer to select the technology and build on a site. The match funding to the government investment is provided by Rolls-Royce and its partners. This advances the design, promise towards site allocation, development of the supply chain, and advances the policy narrative and commercial frameworks for nuclear. The real value of the program is creating a project dynamic and forcing issues to be answered and addressed on a project timescale. UK wants to deploy small modular reactors (SMR) no later than 2030, if not earlier. Rolls-Royce looked at all the things that drive the cost of power output and the cost of construction. They went searching for a construction partner that was not necessarily skilled in nuclear, but one that was skilled in innovative and modular construction. The cost of operations is driven by data analysis and impacts. Rolls-Royce has taken a very cost-driven view of nuclear power to deliver a small nuclear power station. No decision is made if it is thought that it will drive the cost up. Phase One was about firming up cost estimates. Utility partners have stepped forward wanting to engage in this program and private investment funds from other sectors are interested due to the cost of decarbonization. After the next phase, a joint venture will form and equity partners can step in. UK is the first country to legislate for a net zero target across the whole economy. Fundamentally, the power generation footprint needs to be a lot lower than it is today. Over the past five to eight years, UK has decreased emission from 235 grams of CO2 per kilowatt-hour to about 128 today. To get to net zero by 2050, most analysts say that people should double energy generation and delivery to the grid. Nuclear is a proven technology that is low carbon, but it must be affordable and deliverable. Estimates predict that the cost of nuclear power will be just as competitive as everything else. There’s going to be enough need to build enough units in the UK to demonstrate the benefits of the fleet approach and to warrant investigation into the technology. Building in a factory - relative to a big project site build - probably saves you 30-40% of down time. It’s possible, with the scale of the global market, that getting up into 10-20 units around the globe could turn into a supply chain supplying tens of thousands of jobs in the northern UK. One of the visions is for the UK to become a global hook for small nuclear deployment, supply, build, and regulation. The UK SMR is a vehicle to develop a supply chain capability that can service and support multiple technologies, including advanced nuclear, molten salts, and high temperature gas reactors.
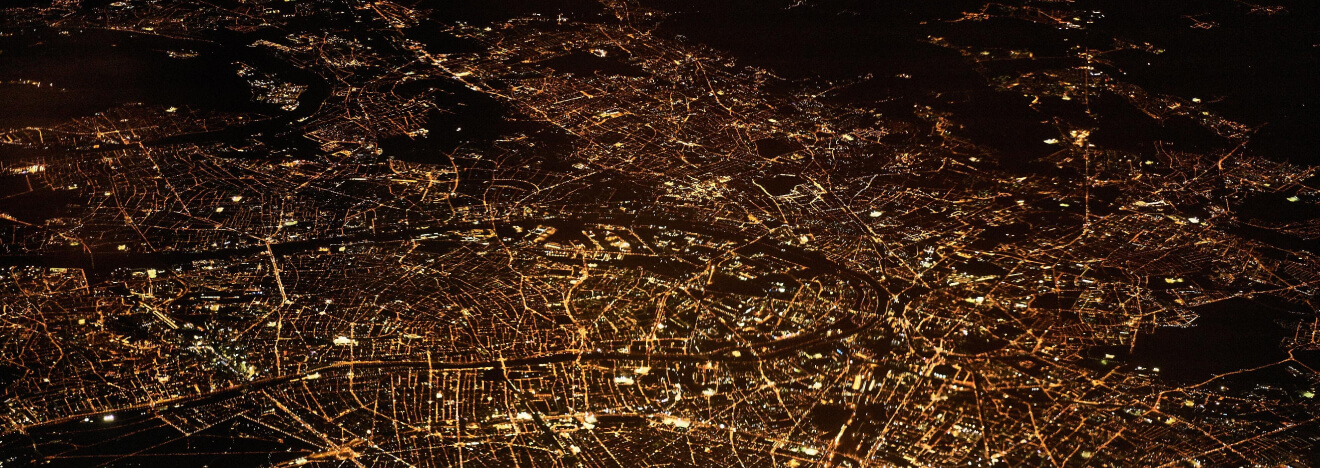