Ep 195: Jeremy Renshaw - Program Manager, Used Fuel and High-Level Waste, EPRI
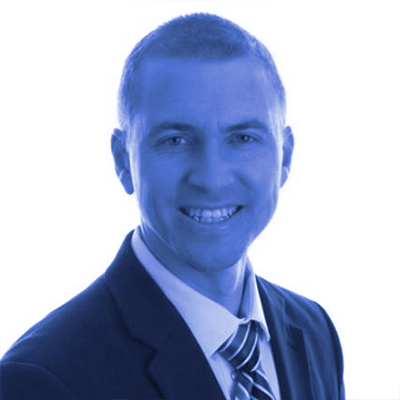
Show notes
Jeremy Renshaw - From Iowa to Brazil to North Carolina (2:44)
Q: How did you end up in North Carolina?
A: Jeremy Renshaw is the Used Fuel and High-Level Waste Program Manager at the Electric Power Research Institute (EPRI) in Charlotte, North Carolina. He is originally from Iowa and received his bachelor's degree from a university in Iowa, during which time he married his wife. The pair soon had two children, all before Jeremy completed his graduate degree. His oldest daughter will be 13 this year; Jeremy says she’s already showing the signs of becoming an engineer. In fact, all of his children are interested in robotics; his daughter placed 6th last year at the World Championships in robotics. Before going to graduate school, Jeremy attended a two-year mission trip to Brazil, where he learned Portuguese. After Jeremy graduated in 2009, during the height of the recession, he managed to find a job in non-destructive evaluation in Charlotte, NC.
Family of Engineers (6:30)
Q: It sounds like your family has an inclination toward engineering and learning?
A: Jeremy says his entire family, both his children and his siblings, always liked math and science. He is one of seven siblings. His older brother was a rocket scientist with the United Space Alliance, one of his younger brothers is as NASA and the other is getting his PhD in robotics. One of his three sisters has her medical PhD in traumatic brain injuries. Jeremy says it’s a friendly competition between all of them.
Non-Destructive Evaluation 9:36
Q: What is non-destructive evaluation?
A: According to Jeremy, non-destructive evaluation is like having a superpower; it gives him the ability to look inside of materials and see what���s there. X-Rays, ultrasounds and eddy currents are other examples of non-destructive methods of evaluation. His specialty was thermography, evaluating heat patterns and distribution of heat flows to find defects. There are positives and negatives to every technique; no method is one size fits all, perfect match. Jeremy says each technique has areas where it is strongest, but other areas where it is weak. Thermal mapping was most useful when testing aircraft components. Jeremy was looking for cracks using vibrothermography. When shaken, differential heating appears in crack faces, delamination and other defects in the component being tested. Sometimes Jeremy could find defects using vibrothermography that no other non-destructive methods could find. He says the key to non-destructive evaluation is understanding materials and their behaviors. Materials are tailored to applications. For example, piles need to be able to withstand high temperatures and be corrosion resistant; airplane components also need to be able to withstand extremely high temperatures but must also be creep resistant. No material is perfect. Jeremy says all materials have flaws and defects. Inspection techniques are meant to identify and correct tiny flaws that could cause failure.
Switching to Nonprofit (13:12)
Q. What did you do after graduate school?
A. Jeremy worked for a nuclear vendor on ultrasonic techniques to inspect reactor internals. He then transferred those skills to the nonprofit sector. Trying to make a difference in the world and working toward a greater good spoke to Jeremy, so he took a job at EPRI. It was the change in mission and the company vision statement that pulled him into the nonprofit sector.
Need for Inspections (14:43)
Q. What is the outcome of determining imperfections in components on the business side?
A. The reason Jeremy does inspections is to prevent failures. He points out that “NDE” has two acronyms: “non-destructive evaluation” and “near death experience.” According to Jeremy, proper non-destructive evaluations prevent near death experiences. Inspections and repairs occur to prevent unplanned outages, broken pipes or bolts, and other failures or to change the material, component or design. Qualification programs are used to demonstrate that certain techniques will find flaws of interests during inspections. But there are no restrictions to using specific types of techniques, rather it is a matter of using any and all techniques to find even the smallest flaws. Both modeling and mockups help prove the effectiveness of inspections. During mockups Jeremy creates intentional flaws that are representative of what might be found in the field. Jeremy has also created artificial flaws to create the behaviors of flaws, without having actual flaws in the material. Other people at EPRI are currently working on virtual mockups. Data from real flaws is used in models to detect virtual flaws in a mockup. The point is to find the probability of detection curves and the reliability that detection will occur. If you have a flaw, you want to be able to find it. Jeremy says half and inch, an inch or longer, detection is much easier. But flaws that are a millimeter or smaller are difficult to find; some techniques will work better than others.
Robots Inspect Spent Fuel Dry Storage Canisters (20:13)
Q. Do you use multiple techniques on one component?
A. Absolutely, Jeremy says. He’s been developing robotic systems to inspect dry storage canisters containing nuclear fuel. The robots inspect the outside of the canisters in the annulus space between the canister and the overpack of a concrete vault that is meant for shielding. The robots are specially designed using 3D printing to navigate the two to four-inch gap between the canister and the vault. The first inspection is typically visual; any part of the canister that is not bright, shiny metal is marked for closer inspection. The next steps include ultrasounds, eddy currents, sampling of canisters, etc. Since these kinds of robots didn’t exist before EPRI started using them for these complex examinations, 3D printing was used during the accelerated development process. 3D printing allows for faster revisions of prototypes and is significantly easier than making changes to the robots in a machine shop. It took about two years to develop the robots Jeremy uses. Robotic Technologies of Tennessee has aided in the production of the robots. Inside the dry storage canisters, the robots must withstand thousands of rads per hour and 150 to 200 degrees Fahrenheit temperatures. All of the electronics are protected and shielded inside of the bodies of the robots to avoid foreign material exclusion problems. The robots are always tethered by two five-hundred-pound cables, so if the robot loses power or gets stuck it can be pulled out of the vault. The smallest robot is about the size of two cell phones stacked on top of each other. Some of the other robots are designed a bit larger, at six by ten inches. One of Jeremy’s favorite robots is a multi-stage robot and acts as a mothership that deploys a second daughtership robot. The mothership robot is about four feet wide, a foot long and a couple of inches tall; the mothership deploys the daughtership once inside the vault. There are also two different modes of transportation for the robots moving around inside the vault: magnetic wheels or vacuum suction systems. Both kinds of robots are capable of moving over 90-degree angles to inspect the sides and the lid of the canisters. Videos of the robots in action are available online on EPRI’s website.
Yucca Mountain (30:30)
Q. Given your experiences, do you feel that dry storage is a problem?
A. Jeremy thinks dry storage is an ingenuitive solution to the problem of not knowing where to store spent fuel. Currently, spent fuel from around the United States is waiting to be transferred to a repository, something that currently doesn’t exist. Yucca Mountain was supposed to be the repository in the United States, but due to political issues instead of technical issues, the project is going nowhere. There are only a couple of countries around the world are making progress with nuclear repositories and Jeremy says that’s because those countries were able to remove some of the political hurdles. EPRI is an independent, unbiased nonprofit, so Jeremy says he stays out of politics and focuses on solving technical issues.
Wet Storage of Spent Fuel (31:53)
Q. What is wet storage?
A. Wet storage typically comes before dry storage. It’s another step in the life cycle of fuel, which begins when you mine the uranium. Then you enrich the fuel and make your fuel. Once fuel has been operated for four to six years in the reactor and squeezed out as much energy as possible, it is then transferred into a spent fuel pool where it typically stays for five to 30 years while radionuclides decay and the fuel cools. Once the fuel falls below a certain threshold, it can be transferred into dry storage. The ideal is for the spent fuel to someday be transported for disposal. Due to delays in the creation of a repository at Yucca Mountain, spent fuel pools began to run out of space and had to be redesigned. The fuel had to be placed closer together than was originally intended, necessitating the addition of neutron absorbers. However, this process doesn’t last forever and replacing every neutron absorbing panels would globally cost billions of dollars, or $25 million per site. EPRI responded by creating the Industry wide Learning Aging Management Program (i-LAMP). The program is meant to take data from plants around the globe and combine neutron absorber materials with the data from the spent fuel water chemistry data and create a database to find trends. The goal is for nuclear plants to rely on each other and foster a system of sister plants that are operating similarly.
Saving Imaginary Lives and Killing Real People (40:11)
Q. How do you balance maintaining margin of safety while keeping operating and maintenance costs low?
A. Jeremy is looking into reactivity depletion uncertainty calculations, meaning the more energy extracted from the fuel the less reactive it becomes. The EPRI benchmarks look at what is the uncertainty of that depletion. In the past an old engineering memo suggested five percent was the correct uncertainty number to use. What EPRI has found through a multi-year study, using actual conditions rather than assumed conditions, the actual numbers of uncertainty are 1.8 to 2.5 percent. In a criticality space the difference between five percent and EPRI’s suggested three percent is huge and offers a lot of operational flexibility. EPRI is working with regulators in the US and abroad to increase acceptance of using more accurate reactivity depletion uncertainty numbers. EPRI’s suggested numbers allow plants to be more efficient, and Jeremy says that increased efficiency often leads to higher levels of safety. He says that this helps prevent radiation exposure for imaginary issues. Similarly, Jeremy says that the way power plants are being operated is counterproductive to the future of climate change. The way power plant operation is going, it is killing real people to save imaginary ones. Nuclear plants are being shut down because of perceptions of safety of imaginary people. Instead, shutting down nuclear plants is killing real people in other countries around the world.
The radiation risk of nuclear plants is mostly based on negative perceptions. For example, Jeremy says that more radiation comes from coal plants than nuclear plants; yet, both are at very small levels.
Next Steps in Nuclear (101:32)
Q. What are the next steps the nuclear industry needs to take?
A. EPRI is working with the Department of Energy and other organizations to create a phenomena identification-ranking table (PIRT). What are the influential factors, what are the knowledge gaps, and how influential are they? For example, an item with a low certainty and a high sensitivity is a big gap. Versus something that is well understood with a low sensitivity; Jeremy says we don’t need to rush to get more data. It allows Jeremy to rank which items he needs to get more data on before making any conclusions. A report will come out next year to help improve safety, efficiency and increase economic benefits. It is important to Jeremy that he helps solve the waste issue so that he doesn’t pass it onto his children and future generations. To Jeremy, it’s all a part of being good stewards of our planet.
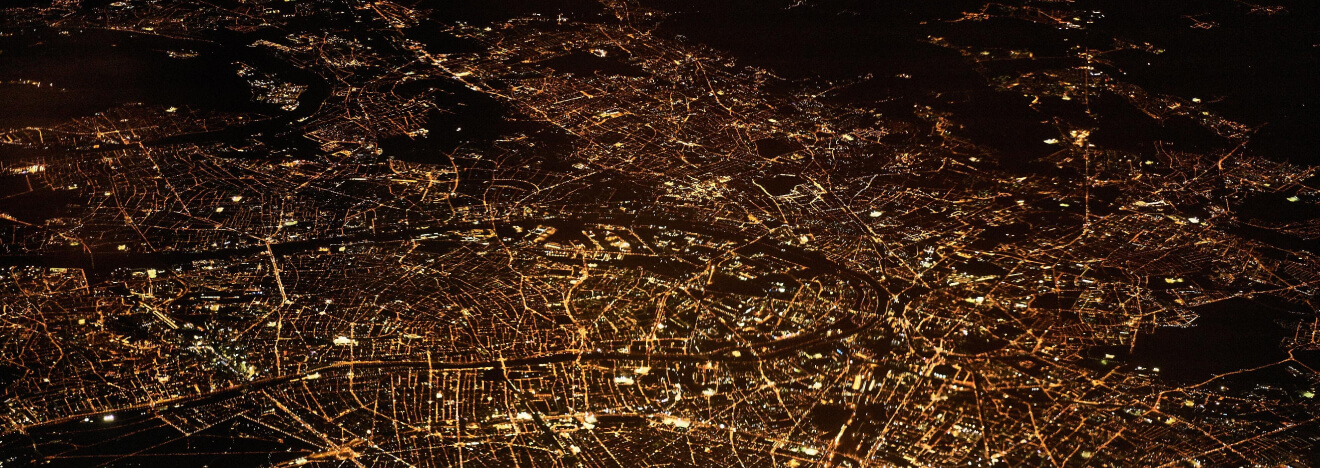