Ep 65: Jay Shaw - Program Director, Nuclear Adv. Manufacturing Research Center
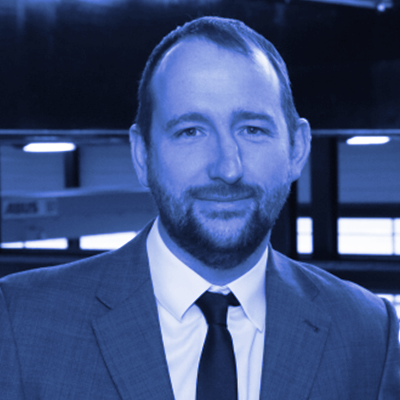
Show notes
Q1 - Traditional vs. Disruptive Manufacturing Techniques
Bret Kugelmass: Where are you from?
Jay Shaw: Jay Shaw is from Leeds, which is now the largest financial center outside of London in the U.K. Sheffield, the location for the Nuclear Advanced Manufacturing Research Centre (NAMRC), was historically and still is very manufacturing focused. Shaw left school when he was sixteen and took on an apprenticeship in manufacturing engineering. He attended an old mining college and got a national certificate, which represented his understanding of the technical delivery of machining and metrology and production planning and control. Metrology is the science of measurement, which is used in inspection of additive and subtractive manufacturing. Disruptive techniques may be used to reduce the cost of the megawatt hour price and U.K. companies are working to be more competitive. Traditional techniques can be used, but it is very difficult to increase productivity. Disruptive techniques could vastly reduce production time. Completing an arc weld for a 24-inch ball plate would take two to three days, but with electron beam welding, this time could be reduced to thirty minutes. This technique removes the human element from the process, which includes checking for defects in between welds. In an arc welding process, an alien material is used to fill the prep which creates residual stress. In electron beam welding, the material is melted together in an electron beam chamber by creating a high density energy zone. As soon as it comes out of the chamber, the weld must be post-weld heat treated to remove those stresses. In a reactor vessel under use, neutron embrittlement affects mechanical properties of the material, which could create a crack that may be exaggerated by the residual stress. Without the use of a filler metal, it could remove the need to reinspect the weld.
Q2 - Developing the Manufacturing Sector in the U.K.
Bret Kugelmass: Tell me about metrology, the science of measurement.
Jay Shaw: The Nuclear Advanced Manufacturing Research Centre (NAMRC), focuses on three main manufacturing processes: welding, subtractive, and additive. The Birkenhead is looking to expand at module manufacturing and NAMRC is also looking at equipment controls and instrumentation (EC&I) and equipment qualification. Even though the U.K. is competitive to the point of making a product, one of the barriers to market for U.K. manufacturing is getting the equipment qualified in the right manner, which could be radiation, thermal, or other testing. NAMRC launched a study to identify the gaps where the U.K. does and does not have capacity and capability. After his apprenticeship, Jay Shaw moved into production engineering and then later a production manager role. A production engineer looks at the drawing of a component, defines the manufacturing process, makes a 3D model, and interrogates a model which drives the numerical tool that goes to a machining or welding tool to manufacture the component. Shaw received his bachelor’s and master’s degrees while working at NARMC, focusing on advanced manufacturing technique. Nuclear ARMC’s mission is to make the U.K. competitive in the manufacturing field by developing new manufacturing techniques and developing people back into the sector, showing the supply chain the possibilities for the technology and technique.
Q3 - Manufacturing Process Optimization
Bret Kugelmass: Have you thought about teaching manufacturing?
Jay Shaw: As an ex-apprentice, Jay Shaw has been given many opportunities. About three-quarters of the NAMRC executive team are ex-apprentices. Shaw mentors nuclear graduates and employees at NAMRC, passionate about sharing things he’s learned along the way to students. Jay Shaw eventually became the Deputy Head of Machining at the Nuclear Advanced Manufacturing Research Centre (NAMRC). The facility is filled with kits, which are bays within a large open room that contain large machinery. The facility has the world’s largest vertical turning lathe and the third largest electron beam welding machine. The team at NAMRC takes an industrial challenge, develop a manufacturing process on the most appropriate size test piece, and look at the technique applied to the test coupon to industrialize it on the manufacturing readiness level. Manufacturing readiness level shows that something can be built at scale. A key process variable for deep hole drilling might be the surface speed of the drill, in rpms, feed, in feet per revolution, and coolant pressure and flowrate. Each process affects the cylindricity, straightness, and accuracy. NAMRC applied a technique called design of exponents in which a matrix of key process variables put against each other at the geometrical outputs are analyzed. This can be used to determined the optimum process. This operation is repeated to determine wear on the drill and determine life and performance.
Q4 - Nuclear Manufacturing Intellectual Property
Bret Kugelmass: What do you do with the information once you develop these manufacturing techniques?
Jay Shaw: The NAMRC has three funding mechanisms that make up the center. The Catapult funding comes from the U.K. government. Collaborative research and development funding is competitively won, predominantly funded by Innovate U.K. and industry together. Commercial funding is also provided to NAMRC, when an organization approaches the NAMRC about solving a particular manufacturing problem and owns the process. Collaboratively funded program intellectual property is shared and Catapult funded projects are property of NAMRC. NAMRC aims to create a roadmap and overlay the manufacturing challenges faced there and bring them back to the teams. In 2016, Jay Shaw was appointed the Business Development Manager for Defense, responsible for looking after the nuclear naval fleet. Shaw worked his way up to Business Director for NAMRC and was recently promoted to Programme Director, making him accountable for delivering the work.
Q5 - U.K.’s Nuclear Sector Deal
Bret Kugelmass: What challenges are you taking on right now?
Jay Shaw: The U.K. recently signed the Nuclear Sector Deal, in which the Nuclear Advanced Manufacturing Research Centre (NAMRC) will play a key role. One program is supply chain development, looking at the business side excellence side of companies in the U.K. and making sure they are fit for nuclear, looking at safety, quality, management and overall business performance. NAMRC also looks at manufacturing innovation. NAMRC’s kits and facilities can help U.K. manufactures be competitive in terms of schedule and cost. The U.K. has some of the largest nuclear new build projects in the world, led by Hinkley Point C, and also one of the largest, most complex decommissioning projects at Sellafield. One of the biggest challenges facing nuclear, internationally, is building a new power plant to cost and schedule. Taking lessons learned from build sites around the world and bringing in diverse teams may bring more success. Other opportunities include decommissioning, which applies to not just nuclear but other energy sectors, allowing lessons learned across industries.
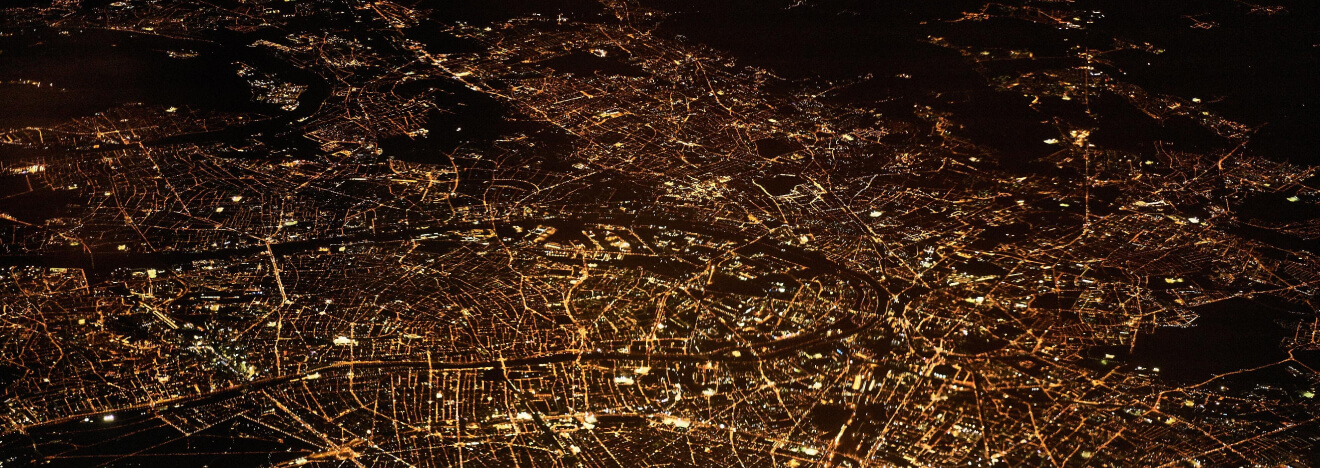