Ep 261: Janne Wallenius - Chief Executive Officer, LeadCold Reactors
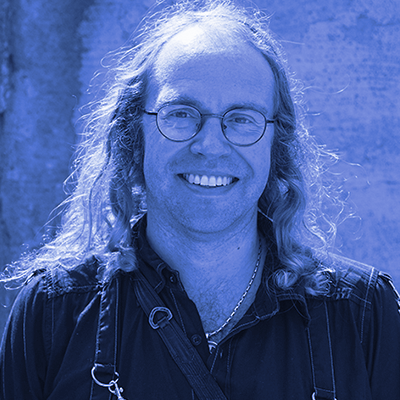
Show notes
(0:46-8:42) Early Lead-Cooled Reactors
(Janne Wallenius introduces his research at KTH in Stockholm, Sweden, focused on nuclear fuel development, and how it led him to lead-cooled reactor technology)
Q: Where did your education begin?
A: At some point during primary school, Janne Wallenius decided he wanted to save the world by developing nuclear energy. He went on to study Engineering Physics at Chalmers University of Technology in Gothenburg, Sweden, followed by a PhD in Fusion from Uppsala University. In 1996, Janne started his post-doc in a research associate position at KTH Royal Institute of Technology in Stockholm where he has been developing lead-cooled reactor technology ever since. At this time, KTH was mainly funded for doing transmutation of nuclear waste using accelerator-driven systems, which were generally lead-cooled. Janne has also been doing research on nuclear fuel development with a main focus on nitrate fuels for plutonium and americium burning. Some fuel types have better density of uranium, meaning the fuel can operate for a longer time in the reactor, however, this is compared to the reference of the industry standard oxide fuel. The major difference in fuels is thermal conductivity. In a normal oxide fuel, the temperature difference between the pellet surface and the centerline of 1,000 degrees C. This difference is reduced to 150 degrees C with a metallic alloy, allowing it to be less sensitive to transients and easier to achieve passive safety. Lead-cooled reactors were first studied for application in American and Russian nuclear submarines in the 1950’s, since the system allows submarines to be very compact. The U.S. program stalled because it was discovered that lead is highly corrosive, while the Russian program interpreted their first test results a bit more positively, launching their first submarine with two reactors in 1963. The system suffered a core melt due to oxidation of the lead after a few years of operation. This led Russia to study and implement an oxygen control system on the same submarine and later launch more submarines with extraordinary performance. To control oxygen in a lead-cooled reactor, the oxygen concentrations must first be monitored with different sensors. Because oxygen is consumed all the time at the free surface, oxygen must be added into the system at a certain rate. This can be accomplished by dissolving lead oxide pebbles into the coolant, exposing the coolant’s free surface to steam, or by use of an oxygen pump.
(8:42-18:05) Development of LeadCold Technology
(How disclosure of Russian lead-cooled reactor technology impacted global research, leading to the creation of Janne’s advanced reactor designs and his company, LeadCold)
Q: Did the rest of the world give up on lead-cooled reactors?
A: Lead-cooled reactors were abandoned until the mid-1990’s when the Russians disclosed their technology and started to have a commercial program. The coolant has a very high boiling temperature, meaning there is practically no loss of coolant due to boiling and good potential for natural convection. Decay heat removal can be achieved in an even more compact form in a lead-cooled reactor than a water-cooled reactor. Passive safety is a strength of lead coolant and if there is a core melt, the lead coolant serves as radiation protection and an in-situ filter. Natural convection testing has been completed in Italy, South Korea, and in Stockholm, Sweden at KTH. The first lead-cooled experimental facility at KTH was set up in the nuclear safety department and has been extensively used for natural convection experiments. While the power is not representative of full power, but the height difference between the heat source and the heat exchange is important to validate the transition from forced flow to natural convection flow and to identify any instabilities.
Janne Wallenius participated in national and European international government-funded collaborations. In 2013, the Swedish nuclear industry got into a bad financial situation and stopped funding his research on nuclear waste transmutation. At the same time, Janne was not able to renew contracts with the European Union, so he could not afford to hire any new PhD students. They had made some progress developing novel technology for lead-cooled reactors, so Janne and his colleague decided to see if they could commercialize what they had made, starting the company LeadCold. Advanced reactors have material problems that have to be resolved. With the exception of sodium, the focus needs to be on material development and qualifying them under adequate conditions. It has taken Janne ten years to go from an initial idea to a steel that he believes will serve well in a commercial environment; this time frame is his first priority. Commercializing a new material requires meeting quality and production requirements. Janne’s tight collaboration with Swedish steel industry has allowed for new material samples to be created with methods that were scalable.
(18:05-27:23) Ideal Materials for a Lead-Cooled Reactor
(Why material science is crucial to the long-term success of advanced reactor designs, with a focus on corrosion and irradiation tolerance)
Q: What are some of the remaining materials challenge that exist in a lead-cooled system?
A: Corrosion is still the major hurdle to commercialization of lead-cooled reactors. Even though the Russians developed oxygen control, it is not sufficient for an ordinary stainless steel to survive in a lead-cooled reactor any longer than a year. Over 20 years, Russia developed a silicone alloy steel that would have improved corrosion tolerance and liquid load. However, this particular type of steel becomes brittle under irradiation, so there is a limited temperature range at which the reactor could be operated. Janne Wallenius and his team decided to go a different track and developed an aluminum alloyed steel based on historical Swedish experience and industrial production. He was able to modify an industrial alumina-forming steel so it could be used in a nuclear reactor without becoming brittle. Retaining the corrosion tolerance while achieving the irradiation tolerance was the challenge. Since the aluminum alloyed steel is not mechanically strong enough to be used as a pressure boundary, so the steel must be welded on top of conventional steels that are approved by ASME as pressure boundaries. In a light water reactor, stainless steel cladding is used on top of carbon steel which is used as a pressure vessel. The same is true in lead-cooled reactors. The final challenge is to prove aluminum alloyed steel can be welded on top of steel while meeting the ASME criteria for the compound system. The first lead-cooled commercial reactor Janne designed was for the Canadian Arctic. In this area, the cost of electricity was so high that operating with a standard uranium oxide fuel with 19% enrichment was good enough to be competitive. At an on-grid market, like the UK or Sweden, an oxide fuel will not perform well enough to be competitive. It’s very difficult to achieve a breeding ratio equal to one in a lead-cooled reactor. Control rods must be introduced to regulate reactivity, causing the core to be much larger. A high density fuel is used to make the reactor more compact to achieve the breeding ratio equal to one. This allows the same fuel to be used for over 20 years. The reactor LeadCold designed for the UK has a thermal output of 140 MW, with an electrical power output of 55 MW. The vessel is 5.5 meter in diameter, compared to a 17-20 meter diameter vessel needed in a water reactor to achieve the same safety level. The plant operates with a traditional Rankine cycle.
(27:23-37:45) Commercializing a New Reactor Reactor Design
(Janne provides an inside look into the process of commercializing a new reactor design and how he plans to bring it to market)
Q: What are the next steps in terms of product creation after you work through the materials issues?
A: Janne Wallenius and his company, LeadCold, have done different conceptual reactor designs. After material issues are resolved, the next step is to build an electrically-heated mockup which can show that the pumps and oxygen control work in an integrated environment. On the engineering side, Janne needs to find the funding to build up an engineering team to complete all the detailed fluid dynamics calculations required to put together a licensing application. Janne has worked with both the Canadian and UK regulators. The Canadian regulator is very agile and has a well-established system for licensing advanced reactors. The shortest time to build a demonstration unit would be in Canada. However, there may be more opportunities in the UK for sites to build a demonstration reactor due to all the former sites that still hold a reactor license and are very suitable. Any novel reactor design needs to be reviewed more carefully than an established design. The designer must be better in mastering all the integrated details of the concept, because the regulator will normally be less experienced. Documentation and technical evidence can make the regulator comfortable that the technology will work. This requires the engineers to be very detailed in the whole process, both on the engineering side and in written documentation. The regulator is not only protecting the public, but also the operators at the reactor. Each of the 200 systems in the plant must be described at a level that makes the regulator comfortable. Janne hopes the reactors can be built in an automated factory as much as reasonable to allow the reactor operators to order a reactor and get it delivered in 24 months. This allows a completely different relationship between the utility and the vendor. This allows a much larger range of power utilities to become nuclear power plant operators. Nuclear power plays a necessary part in combating climate change so these reactors must be rolled out at a fast pace. A minimum goal would be to produce one-third of the world’s electricity with nuclear power before the year 2050.
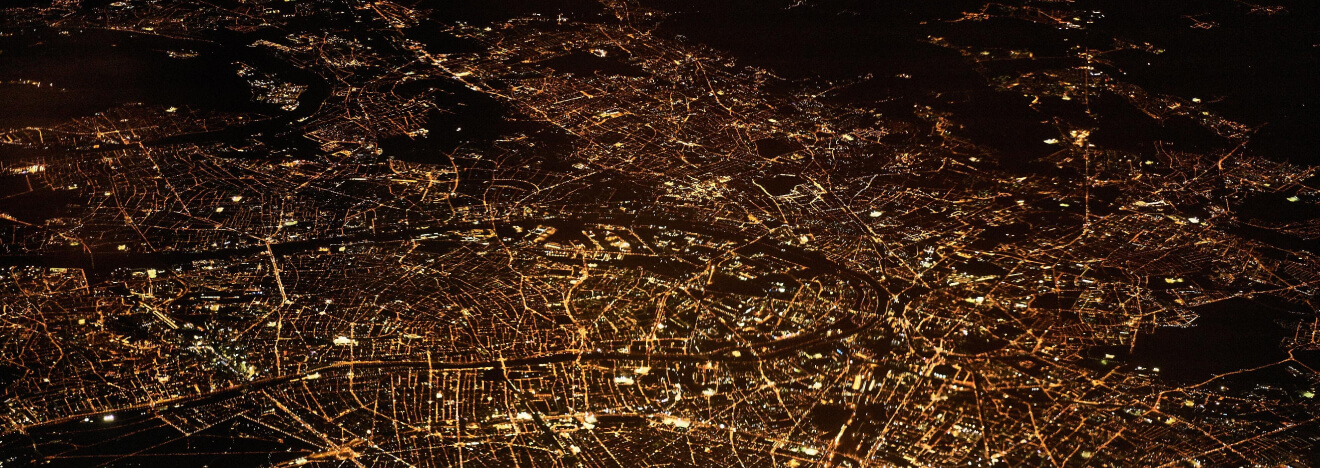