Ep 09: George Griffith - Small Modular Reactors, Idaho National Labs
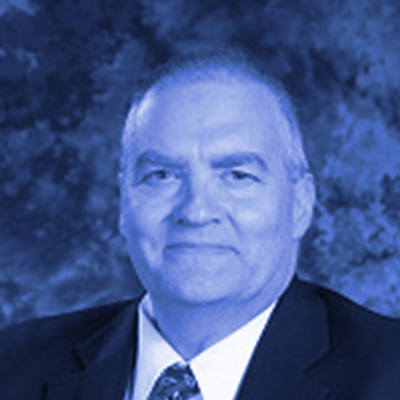
Show notes
2:26 - Making Fuel for Boiling Water Reactors
Bret Kugelmass: How did you get involved in the nuclear space?
George Griffith: George Griffith studied nuclear engineering at Iowa State University and spent a summer working at Argonne National Lab in Chicago, where he was engaged with how to design things and tools used to make things. While at Argonne, Griffith worked at a pulse neutron source, which uses an accelerator to hit a heavy metal target to produce neutrons for scientific use. This led Griffith to pursue a PhD at North Carolina State University, focusing on computational methods and Monte Carlo. After finishing his doctorate, Griffith spent a couple years at Los Alamos National Lab before hiring on with General Electric where he started building nuclear fuel and was in charge of safety and quality for nuclear instruments. Uranium hexafluoride is heated up and turned into a gas, then converted into uranium dioxide, which is the material that goes inside the fuel rods. These are shaped into cylinders, loaded into cladding, welded up, and placed into bundles. This fuel was used for boiling water reactors (BWR), and had lots of enrichments and levels of poison to make sure they operate well in a boiling water environment. In a BWR, water comes in solid at the bottom of the reactor and heats up and turns into steam at the top of the reactor. This great change in density creates lots of fissions at the bottom and less as you get to the top. Letting that run without control creates an uneven distribution of power. Poison is added differently at the top and bottom of the core to control the power. The poison is a very small quantity of an element that wants to absorb the neutrons very aggressively.
7:06 - Industry Experience at Cooper Nuclear
Bret Kugelmass: What did you do after making fuel at General Electric?
George Griffith: After making fuel, George Griffith transitioned into working on design of reactors, specifically the design of the fuel, poisons, and enrichments. Griffith then moved into industry to work as a reactor engineer at Cooper Nuclear in southeast Nebraska. Communities appreciate the value the nuclear plant adds to the economy. As an engineer, Griffith would find out what happened at the plant overnight, perform triage on issues that came up, and work on longer term projects like reloading and maintenance. At this time, the reloading process what approximately 30 days that started with turning the reactor off, scramming it, and cooling it down. The reactor head is removed and the core is disassembled to access the fuel. A gantry crane is used to reach approximately 80 feet down. During reloading, there is usually double the staff on-site; at Cooper Nuclear, there were around 2,000 people on-site. Maintenance is also performed during the reloading outage, such as replacing turbines or generators. The plant had an outage center that monitored all activities during the outage and determined how the schedule was changing. During outages, staff usually puts in 12 hour days.
13:50 - Reactor Sustainability Program at INL
Bret Kugelmass: What happened after you worked at Cooper Nuclear plant?
George Griffith: After working at Cooper Nuclear, George Griffith moved to Idaho National Lab to work with the Light Water Reactor Sustainability (LWRS) program. The U.S. has around 100 light water reactors and these plants are reaching the point to be licensed from 40 to 60 years and a relicensing from 60 to 80 years is under consideration. The Nuclear Regulatory Commission (NRC) considers things like whether components are wearing out and the overall reliability. Some large questions remain, such as whether the steel in the vessel has changed with exposure to hot water, corrosion, and gamma rays over a span of 60 years. Instrumentation and nuclear fuels are also considered whether plants can operate safely and efficiently. They must also consider than standards, costs, and the size of plant security forces have gone up.
17:19 - Idaho National Lab Projects
Bret Kugelmass: What other work have you done at Idaho National Labs?
George Griffith: George Griffith worked with Idaho National Lab’s (INL) Advanced Test Reactor (ATR), the largest test reactor in the U.S. Experiments are placed in the ATR to prove that materials will last, fuels have been designed properly, and instrumentation can be tested in new radiation. INL’s primary customer at ATR is the U.S. Navy, but is also widely used by universities and companies to test their concepts. Their fuel cycles are around 80-90 days, so they are constantly in outage and designing cores. Griffith also did some work with advanced manufacturing, such as 3D printing of titanium for nuclear applications. Individual pellets have been made out of one homogeneous material, but they are looking into print pellets with different layers, which would allow for variations in enrichments, poisons, and structures that help heat escape. Accident tolerant fuels that result in less stress on the system if there were to be an incident at the reactor. The current fuel being used has been developed for 50 years, so it is a challenge to replace an optimized fuel with a new fuel that is better in every way.
21:43 - Current State of Small Modular Reactor Technology
Bret Kugelmass: What is an SMR?
George Griffith: An SMR is a small modular reactor, defined by the International Atomic Energy Agency (IAEA) as a reactor less than 300 MW. A typical reactor in the U.S. is around 1,000-1,200 MW. Two of these reactors are currently being built in the U.S. South, and two other projects are on hold. To build one of these projects requires multiple billions of dollars. The size of the project puts utilities at risk since it would take up a significant percentage of their industry. The idea of SMR’s is to scale nuclear reactors down. Traditional reactors are built on-site and require steel, concrete, and components to be brought in during construction. The SMR concept is to be built in a factory, which would take a lot of the economic risk to a place where it can be more easily controlled. NuScale is the most advanced SMR design team in the U.S. right now. They are designing a 50 MW water-cooled and water-moderated reactor that can be built in a factory. NuScale is also considering how to make their plants hypersafe, in the sense that, if there was an incident, operators would take their hands off the controls and leave the reactor and the reactor would be alright. NuScale has been working on their development for about 15 years. Building the large plants on-site with contractors has challenges and risk, since there have not been many reactors built in the U.S. SMR’s aims to fix the economics, the deployment issues, and build issues. Each designer comes up with a different solution to that challenge. Others are using advanced reactor designs, such as molten salts and molten leads. NuScale is working with the Nuclear Regulatory Commission (NRC) towards their application. Idaho National Lab (INL) may host the first nuclear power plant using NuScale technology. Utah Association of Municipal Power Systems (UAMPS) is looking to own the reactor at the INL site to help them supply energy into the system. The benefit of having this UAMPS site at INL is that INL knows the area, including seismic, water, animals, etc. since they have been in Idaho for over 50 years. George Griffiths translates between different teams, including siting, engineers, and others. In the next couple of years, the plant will be under construction at INL.
33:03 - How Economics Drive Nuclear Technology
Bret Kugelmass: How do you see nuclear technology evolving over time?
George Griffith: It seems that the really large plants are particularly difficult to build. If the four plants in the South can be successfully pulled off and proved that they are economically viable for the companies that bought them and the communities that supported them, there will probably be a few more. If those plants don’t deploy, the U.S. is left with small modular reactor (SMR’s) concepts. While large plants need specialized transmission resources, SMR’s allows for deployment in different markets and replacement of coal plants, which are typically smaller. Everybody is waiting for the first SMR successful deployment to prove it works and can be done.
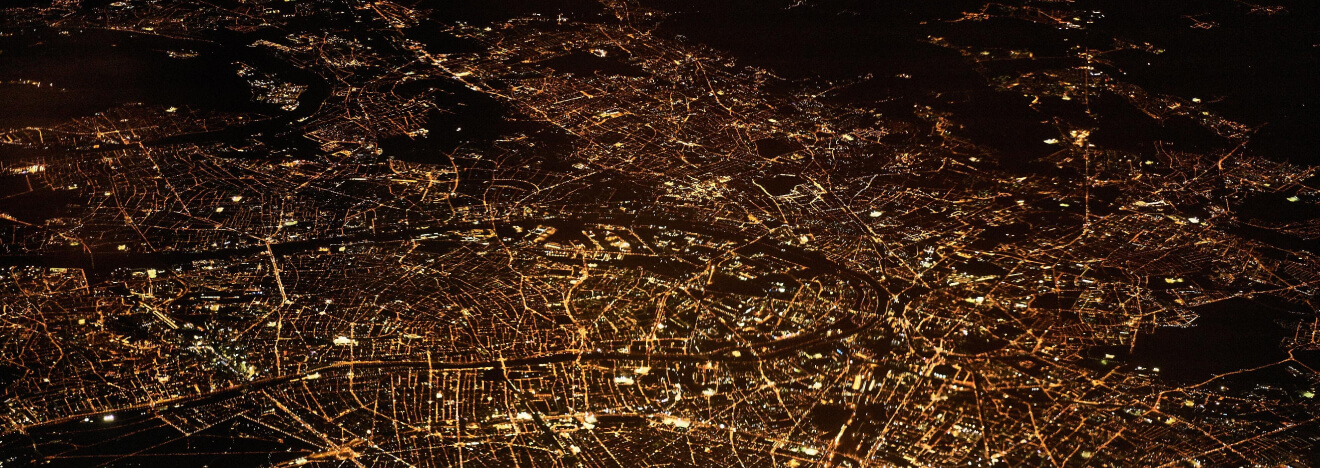