Ep 80: David Gandy - Advanced Manufacturing Expert, EPRI
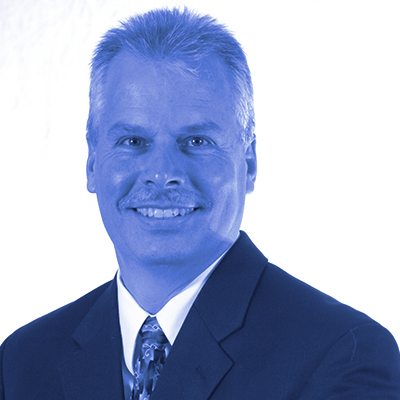
Show notes
1 - Metallurgy and Nuclear
Bret Kugelmass: How did you get started in the nuclear space?
Dave Gandy: Dave Gandy’s background is in metallurgy, which he studied at North Carolina State University, leading him to start out in the welding area. He moved over to work for the Electric Power Research Institute (EPRI) in 1996. Dave Gandy had done an internship with J.A. Jones Applied Research working in the welding area, mostly focused on manual stick welding or semi-automatic gas tungsten arc welding to support pipe replacement in the boiling water reactor. In general, most piping in nuclear plants have welded joints. Quality inspections are performed on welds with non-destructive evaluation (NDE) tests, usually ultrasonic, which can detect anomalies or manufacturing defects. Inspections are completed before startup and at set intervals throughout the life of the plant. When Dave Gandy started with EPRI, he focused on a lot of fossil related activities, specifically metallurgy in the high temperature area. The team looked at different components to determine material fatigue or failure methods. In a fossil plant, the main concerns are fatigue and creep, due to the exposure of time, temperature, and stress. The alloying elements, such as molybdenum or nickel, give materials the strength and capability to perform as designed. In general, the conservative nuclear industry tends to stay with well-known, well-performing alloys, unless a revolutionary material comes along.
2 - Advanced Manufacturing Techniques
Bret Kugelmass: Is manufacturability an issue when dealing with different alloys?
Dave Gandy: Certain manufacturing tools are used for much stronger alloys and may need to be bent at a different radius or string rate to get it to the final component size and geometry. Typical fossil plants in the U.S. operate around 1050 degrees F. In 2008, Dave Gandy moved into the Electric Power Research Institute’s (EPRI) technology innovation area, which looks into long-term research development. Technologies at the time included nanocoatings for insulators and power line cables, which minimizes ice build up. From a power plant perspective, there will be a few components that are produced with additive manufacturing, also known as 3D printing. Some of these components could be reactor internals, small valves or pumps, or replacements for obsolete components. When a part goes through additive manufacturing, it typically goes through a solution anneal at a high temperature with water coolant or a hot isostatic press. Tensile properties are generally quite good, but toughness tends to lack in this process. This could be due to impurities in the atomization process. EPRI is working on putting together a two-thirds scale small modular reactor (SMR) and is making very large girth welds with electron beam welding. Electron beam welding can be done in a single pass and does not require any filler material, and there may be no visible evidence of the weld after it goes through a final heat treatment.
3 - Electron Beam Welding
Bret Kugelmass: What are the advantages of electron beam welding’s narrower heat affected zone?
Dave Gandy: The heat affected zone has different properties from the base material. Alloys go through solution anneal or heat treatment to bring it back to a similar property or microstructure of the base metal. The Electric Power Research Institute (EPRI) believes electron beam welding can eliminate about 90% of the standard welding time on a typical large girth weld. Small modular reactors (SMR) and Gen IV reactors must be made in a different way, by being physically made in a shop environment and then shipped to the plant for installation. Many of today’s large reactors are large forgings made in Japan, Korea, China, and other places and shipped to the U.S. Due to the size of the reactor vessels, the forging process requires a very large forge and a massive ingot. Only a certain number of vendors can make these components. Electron beam welding has been around for about 50 years and typically requires being placed inside a large vacuum chamber. EPRI is looking to build one of these chambers. Dave Gandy has been working on a project in powder metallurgy since 2010, which can be combined with hot isostatic press. Powder is placed inside a can, sealed with a vacuum, and placed in a hot isostatic press, which produces a solid material with the geometry of whatever component you were trying to make. Components that could be manufactured with this process include large valves, pump housings, reactor heads, and steam generator heads. EPRI is working with industry to bring forward a consortium that will help install a large hot isostatic press.
4 - Powder Metallurgy Hot Isostatic Press
Bret Kugelmass: Are there other industries that have expressed interest in advanced manufacturing techniques?
Dave Gundy: The offshore oil industry is ahead of the nuclear industry in terms of advanced manufacturing, specifically powder metallurgy hot isostatic press (HIP). In 2010, the Electric Power Research Institute (EPRI) spent a lot of time getting ASME qualifications in place for this process. Newer nuclear reactor designs are going to operate at higher temperatures than are currently being used. Higher operating temperatures require better ways to manufacture some of these components and some casting and forging technologies may not work for certain applications. There are a number of advanced nuclear plant companies that are starting to look at how specific components are manufactured and how to put their technology in place. The U.S. does not have the infrastructure together today that they had twenty or thirty years ago to perform all the manufacturing, so there must be other ways to assemble the components. EPRI made a number of components early on with 316L stainless steel; during manufacturing, all would have good strength, but some would have poor toughness and some would have good toughness. Strength is the ability to hold a particular structure in place. Toughness is the ability to absorb impact. The 316L powders were producing a variety of different results in toughness based upon how the material was being handled. The team determined that, if they could control the oxygen levels in the powder, they could control the toughness. This control is done during the atomization process.
5 - Additive Manufacturing in Nuclear
Bret Kugelmass: Is there any way to actively rip the oxygen off the outside of the 316L stainless steel particle with some other chemical process?
Dave Gandy: Some vendors are looks at ways to actively rip the oxygen off the outside of the 316L stainless steel particle, but this process does not currently exist. One of the areas the Electric Power Research Institute (EPRI) will be focusing on over the next five years is additive manufacturing. There may not be a large number of power plant components made with this process, but there are certain components to which the technology would lend itself well. There must be good specifications for additive manufacturing that allow nuclear quality components to be made. Only one alloy is being looked at right now, but there are seven or eight alloys used routinely throughout the power industry that must also be developed. Ferritic alloys are more susceptible to oxygen pickup, so they must understand oxygen issues and how to process them. Moving toward advanced generation nuclear components, there will be higher temperature alloys. Nickel-based alloys rely on cobalt to provide some level of strength and capability, but cobalt is not a good actor in a nuclear environment, so new nickel alloys must be developed. When activated, cobalt can become a radiation source. There will be alloy challenges in erosion resistance, oxidation issues, and creep performance. Dave Gandy is a big believer in innovation; the U.S. will rise to the top in advanced generation nuclear.
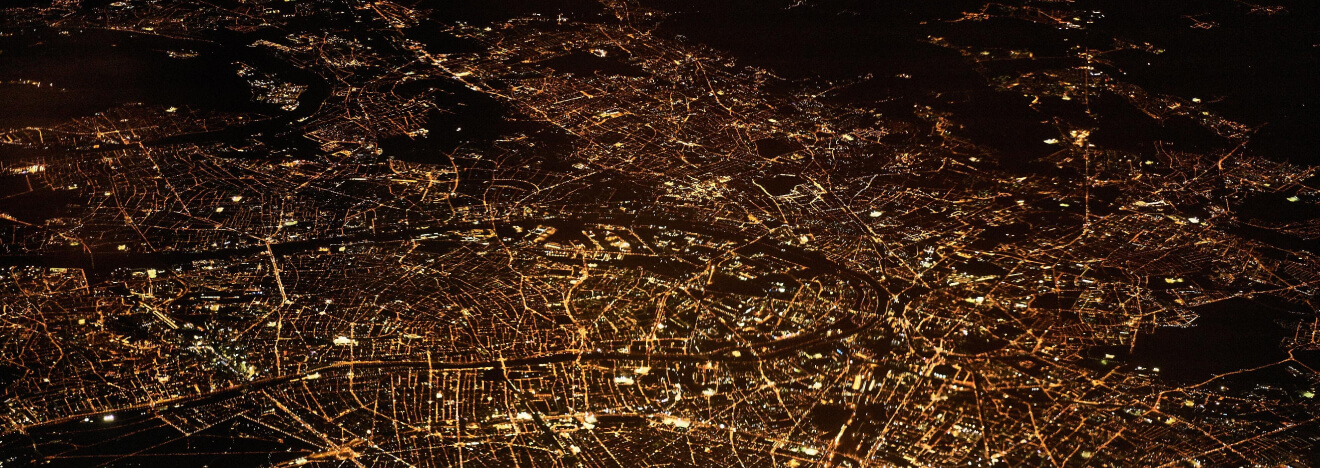