Ep 78: Dan Wells - Water Chemistry Expert, Electric Power Research Institute
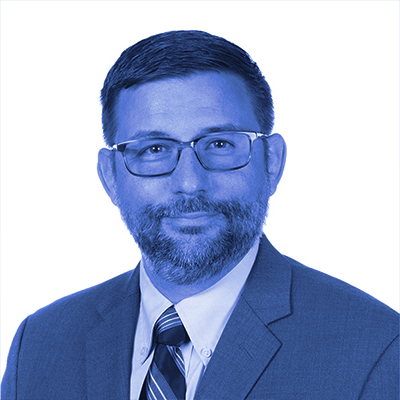
Show notes
Q1 - Water Chemistry in Nuclear Power Plants
Bret Kugelmass: How is your section of EPRI organized?
Dan Wells: Dan Wells is the water chemistry expert at the Electric Power Research Institute (EPRI), working on anything water touches at a nuclear power plant, such as water used for ultimate cooling and water that gets heated to generate electricity. Wells went to Auburn University to study chemical engineering and completed an internship at a nuclear power plant. Wells went back to university and decided he wanted to be more of a research setting than an industrial setting. Actinide work exposed him to working with radioactive materials which influence his experience and eventually got him back into nuclear energy. During graduate school, Wells did neptunium chemistry work at Argonne National Lab. He got back into nuclear in engineering support from a contracting side. As more is discovered about chemistry, it may be discovered that adding zinc to the primary coolant helps with cracking issues or adding a dispersant to the secondary side helps manage corrosion products. Most chemical addition systems are being added continually to the coolant and is monitored continuously. When you want to understand the corrosion products are in the coolant, you can hook up an apparatus to the coolant system that pulls a sample of the rust from the system for analysis. The primary chemistry that is changing over time is the oxides on the material, since metallic material corrodes over time as it is exposed to water. Chemistry is modified to slow that process, by altering the metals used and changing or purifying the coolant.
Q2 - Effects of Corrosion in Reactor Coolant
Bret Kugelmass: How do they get the water for the primary side initially?
Dan Wells: Any power plant, including nuclear power, pulls water from whatever source it is near. If it is by the sea, it may pull from a municipal source and not have to purify it as much; some plants have desalination plants on site. If the plant is on a river, the water is pulled from the river and passed through several cycles of purification until it was ready to be used as primary coolant. A pressurized water reactor has about four loops of water, each having higher purity. General corrosion releases primarily nickel and iron. When nickel goes into the core, it gets activated and turns into cobalt-58 which has a high energy gamma and produces a lot of the radiation fields in a nuclear plant. To get rid of the cobalt-58, you can purify it or reduce its deposition. High temperature water circulates quickly, so the cobalt-58 wants to go back into the water and deposit where there are heat transfer processes happening. Many plants inject zinc into the primary coolant, which competes with the cobalt-58 and gets incorporated rather than the cobalt-58. Cobalt-60 is a product of cobalt and primarily comes from an impurity in stainless steel and anytime you purify a metallic alloy. Some also comes from a high strength alloy call stellite, used in hard facings and valves. As the valves get turned, some of the cobalt comes off and gets in the coolant, getting activated and deposited. Over time, the corrosion layer between the base metals and the water gets more stable and protective. Initially you have a lot of corrosion.
Q3 - Controlling Radiation Fields
Bret Kugelmass: How has our understanding of water chemistry in reactors changed over time?
Dan Wells: If you go to a standard U.S. nuclear power plant and follow around a chemistry technician, they will be taking samples of water daily to give one data point. This requires a lot of labor and a lot of cost. Dan Wells is working on automating that process. Outside of nuclear power, a lot of plants are monitoring water and have instituted technologies that can give them a data point every 30 minutes or every hour. The Electric Power Research Institute (EPRI) is working to understand the current technologies, provide the industry with an understanding of how they operate and what the maintenance requirements are so they can get these out in the field and help with the cost requirement. If they can understand events that cause a spike in impurity or corrosion product, there is a much better chance of actively controlling the chemistry. If corrosion products are expected, you can flush the system first or send the water through the purification system. With only one data point a day, you may or may not catch the changes in corrosion products. There were some events in which primary coolant was leaking past seals that led to precipitation of boric acid outside of the primary system. Chemistry was not the fault, but chemistry was the indication. Plants have had numerous experiences with hot particles, such as a cobalt-60 particle that made it into the core and is a radiation source. The main concern is dose to the worker, which may require extra shielding or an attempt to flush the particle. Dose rate fields change how you do your work. Boric acid has a high cross-section, which describes the strength of the interaction between neutrons. In a pressurized water reactor (PWR), boric acid is used and the concentration in the system must be controlled to control fission.
Q4 - Boric Acid and Flexible Power Operation
Bret Kugelmass: How is the boric acid changing over time?
Dan Wells: Boron-10 turns generates lithium-7 in a radiochemistry process. A majority of the boric acid removal is through the purification system. In a fuel cycle, you start with fresh fuel so you need more boron to slow the fission. Over the cycle, the boric acid solution goes down through purification methods, called the boron letdown curve. Before you start a cycle, you design your boric acid letdown curve to match your core design. There are detectors monitoring the neutron flux throughout the cycle and many plants are moving towards flexible power operations, not operating at base load. This can be done by increasing the boric acid concentration, adding more to the coolant to slow down the flux, or by inserting the control rods. If you insert the control rods to slow fission and want to come back up, the core does not look the same and your boric acid can be adjusted to manage that. How quickly you can reduce power depends on where you are in the cycle, how the control rods are designed, and other factors. Changing power with chemistry takes longer and works better with lower frequencies. Boric acid is the main chemical shim used in pressurized water reactors (PWR). Western-design PWR’s add lithium to the water to manage the pH and Russian PWR’s add potassium to manage pH. The Russians also inject ammonia that decomposes to hydrogen which helps with radiolysis in the water. CANDU reactors use heavy water, which is deuterated water which also has a high cross-section for neutrons. Deuterium is used to control fission and lithium is used to control the pH. Boiling water reactors (BWR) use void fraction to control the fission, where the steam is and where the water is in the core. The density of the water impacts the fission rate and where the neutrons go. Control rods are used more frequently in BWR’s. They add zinc for radiation field reduction, but don’t have as much nickel so they don’t have as much cobalt-58. Hydrogen is also used to control radiolysis and mitigate cracking. Cracking is a concern in vessels, piping, and all internal components that are costly to replace.
Q5 - Innovation in Water Chemistry Technology
Bret Kugelmass: Are there other chemistry concerns in boiling water reactors (BWR)?
Dan Wells: There is a dryer in the top of the reactor before it goes over to the turbine, but there is still some moisture carryover in the steam. If you have water, you can carry over anything in the coolant, including the radiocobalts and end up with activity in the turbine parts of the BWR. A boiling water reactor uses almost purely water, with some zinc, in the coolant. Moving as much to automation and advanced technologies is a major initiative at the Electric Power Research Institute (EPRI). There are instruments that just sit in the flow and give you dissolved hydrogen concentration. If you want to understand nickel and iron concentration, you have a combination of dissolved species and some particulate concentration. There are a number of different technologies being applied and picking the right one for the needs of the power plant is a focus at EPRI. EPRI brings an assembly of instruments to plants to demonstrate new technologies. This lets EPRI know how the technologies work in the environment they need them to work and also determine maintenance requirements. Quality assurance programs are the main thing driving maintenance requirements. Regulatory space for water chemistry is pretty light in the U.S., but is very country dependent. Boric acid is included in the design for fission and lithium is included for pH, but no other chemistry is included in U.S. regulatory documents. EPRI has a set of water chemistry guidelines developed and updated by the industry based on R&D and the utilities have committed to meeting the guidelines. This document includes action levels and sampling and monitoring frequencies.
Q6 - Automated Chemistry Control
Bret Kugelmass: What other type of R&D activities does EPRI engage in?
Dan Wells: In addition to the kind of analysis technologies, the water chemistry department at the Electric Power Research Institute (EPRI) has started an initiative working on advanced data analytics. EPRI has a software package of data analytics that continually analyzes the plant data and sends alert to check on parameters. With much better data, EPRI is working to develop better algorithms to analyze the data and make the analysis even more automated. Advanced plants and small modular reactors (SMR) have automated chemistry monitoring and control in their designs. For a parameter like pH where you are trying to keep it in a range, a purification bed could come on to help remove lithium, then later the purification bed could be removed from the system. Algorithms are analyzing that data continually to look for issues and changes in control and the actual plant maneuvers to that data. Different molten salt coolants change the type of analysis you want to do. Understanding the chemistry of molten salt is not determined at all and the materials have not been finalized yet. EPRI has not historically worked in the gas-cooled reactor space as it relates to water chemistry. There are issues with purifying lithium-7, so EPRI is doing work to qualify that it would be safe to switch from lithium to potassium, which could bring a lot of potential savings. EPRI is also looking into film forming products that help provide another impediment to water corrosion, which would eliminate having to mediate the other issues down the line. The fossil fleet already has automated chemistry. The technologies are there to close the gaps in nuclear and reduce the overall cost of operating the plant.
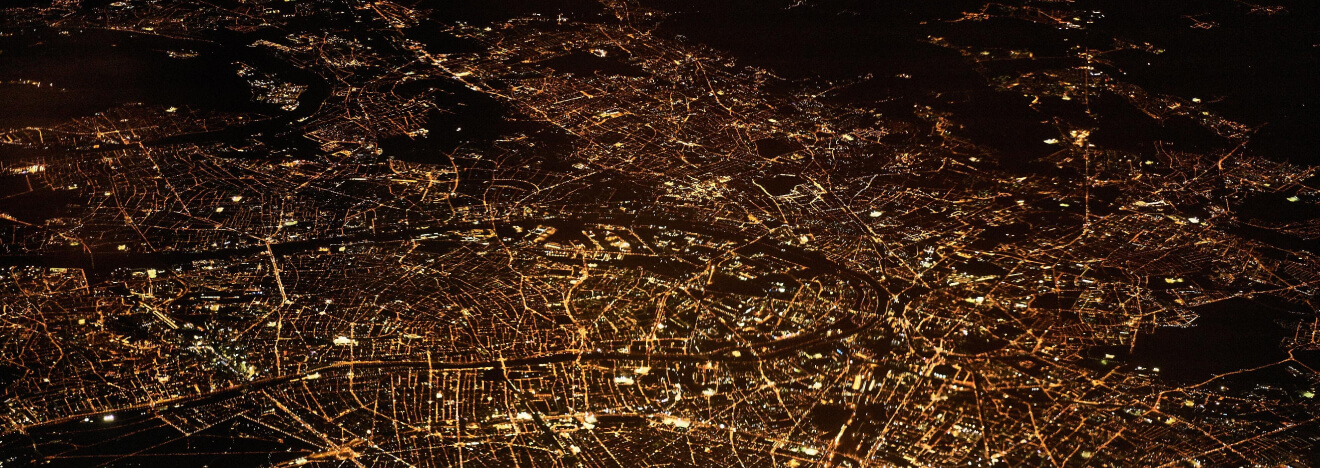