Ep 98: Curtis Van Cleve - Vice Pres., Components, Repair and Replacement, Framatome (US)
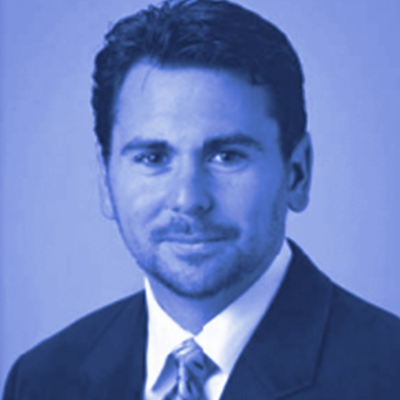
Show notes
1 - Nuclear Reactor Recovery Team
Bret Kugelmass: How did you get into the nuclear space?
Curtis Van Cleve: Curtis Van Cleve attended the Virginia Military Institute, an engineering school that specializes in mechanical-type engineering programs and sets students up for officer commissioning into the military. Van Cleve did engineering around turbomachinery and power plants systems in preparation to do Navy Nuclear. When medical issues prevented him from pursuing that career, Van Cleve connected with the commercial nuclear fleet at B&W, which became Framatome, transitioning directly into reactor service engineering and tool and component engineering. Later, Van Cleve transitioned into leadership roles, including design of components and installation. He was a member of the recovery team that would travel to plants and recover from issues the power plant had, such as damaged components. Over time, fuel assemblies will stick with the upper internals. The upper internals has a very close fit to the core; the reactor core must be kept very stable. During disassembly, the internals are captured in tension to the vessel, but sometimes the pins on the upper internals get damaged and the fuel pulls with the internals. Van Cleve designed tooling emergently, qualify it in a mock-up facility, and implement the recoveries on-site. Another emerging issue was steam cuts on the reactor vessel, which occur when a mating joint is not completely dry during startup and steam escapes, causing erosion of the metal.
2 - Reactor Repair Design
Bret Kugelmass: How is weld build-up used to repair steam cuts?
Curtis Van Cleve: Steam cuts look like erosion on the bottom of a riverbed and it must be repaired as part of asset management. During recovery work, Curtis Van Cleve learned how to have a risk-based, cool composure and a good working relationship with both utilities and craft. He participated in a recovery project in the Southern U.S. which involved repairing a damaged portion of the internals in the instrumentation column. This required years of mock-up and training with 20 underwater construction divers to prepare for this process. A couple different components were patented because it is not easy to weld under boric water. The boron is used as a neutron control agent, but becomes problematic in repairs because it makes welding difficult. Van Cleve supported a crushed core, which is damage to internals during installation, and his team had to stabilize the fuel assembly and design a carriage to move it. Respect for the core itself must be at the highest level. The most frustrating projects are the small projects that are less complicated but have high financial implications, such as schedule impacts. For more complex problems, Van Cleve and his team ran 24/7 with cross discipline between components, welding engineers, structural analysis, and thermohydraulics. This position provided Van Cleve with the field and implementation experience working with both the utilities, workforce, and engineers to deliver projects. This led him to more complex projects, such as reactor pressure vessel head and steam generator replacements, eventually running the organization that is responsible for asset management of the nuclear steam supply side (NSSS) components of Framatome Services.
3 - Material Reliability Program
Bret Kugelmass: How does a plant engage with Framatome Services?
Curtis Van Cleve: Curtis Van Cleve’s team at Framatome Services is asset management. In the life cycle of a reactor vessel, the owner must think about how components are maintained, how to extend and assess its life, and how to replace it at the end of the life cycle. There are a couple dozen critical components on the nuclear steam supply side (NSSS) along with some peripheral components. Framatome will do the probabilistic risk assessment (PRA) for where failures are going to be, down to welds and bolts-level detail. The bolts that hold the internal core structure together are not safety-related to loss of coolant accident (LOCA), but are instead a foriegn material issue. These bolts are out-of-reach, highly activated, and were originally welded to a cross member; there are anywhere from 900-1,400 bolts in a traditional core support. Each plant has a material reliability program (MRP) that follows an industry-wide, agreed upon frequency of monitoring of components. If there is excessive repair, a non conformance report is issued and goes through an engineering, risk assessment, replacement, and repair procedures. Nuclear is researching how to get from need-based maintenance to truly predictive maintenance. Predictive maintenance looks at sensors that provide little bits of information that humans can correlate to future failures. Cost of maintenance can go down by being smarter about maintenance frequency.
4 - Component Stress Relief Techniques
Bret Kugelmass: What are some of the components that need to get refurbished or replaced the most frequently, and the least frequently?
Curtis Van Cleve: Curtis Van Cleve has a tremendous amount of respect for the engineers from the 1930’s and 1930’s, as well as the eventual commercialization of the Navy Nuclear in the 1950’s and 1960’s, because the designs are incredibly robust. The wear seen on the internals today, after 40 years of operation, are incredibly minimal. Wear seen on pump internals is on the scale of hundred-thousandths and ten-thousandths, typically cracks in heat affected zones. Cavitation peening is used to create a vapor bubble; when it contacts the surface, the implosion forces dimple and relieves the stress in the material. Heat, shot peening, and cryogenic freezing are other stress relief techniques. Framatome has done work with the government on laser powder overlap, which may be used as stress relief in the future.
5 - Value of Existing Nuclear Power Plants
Bret Kugelmass: What did the U.S. do right in the 1960’s and 1970’s that they are performing better and cheaper than ever, so many decades later?
Curtis Van Cleve: When the nuclear power plants were built in the 1960’s and 1970’s, the cost of land was a lot cheaper and the infrastructure built around the plant was, in general, cheaper. Today, all that infrastructure is paid for. Challenges at V.C. Summer and Vogtle surround documentation, getting components in, and the cost and burden of the nuclear processes. When considering power generation, base load, credits for having 24/7 availability, nuclear plants in the U.S. has a capacity factor of over 96%. No other power source has that type of capacity factor. In the middle of a storm in Texas or an arctic vortex up North, nuclear plants keep running. The plants in the U.S. today need to be cherished as a national resource. They don’t need fuel to come in every day; there is 18 months of fuel sitting on a nuclear site, which is an asset to the American people and the national security of the country. When Framatome Services replaces components, they are replaced with more safety margin, more features for industrial safety, radiological upgrades, and more resistant alloys. The manufacturing process today, compared to the 1960’s, is better controlled, more understood, and more automated. This allows for a better fit and the next generation of components will not see the cracks original components see now.
6 - Generational Handoff of Nuclear Technology
Bret Kugelmass: How do you see the nuclear industry changing and what do you hope to see in the next era of nuclear and power supply in general?
Curtis Van Cleve: It is time for the next generation to take the nuclear fleet and own it. The existing fleet, of an appropriate design, need to get through a second license renewal and through another 40 years of operation. At that time, in parallel, the next generation of reactors and fuel should be looked at. In the next generational handoff, the technology should have accident tolerant fuels (ATF) to fix coping time issues, licenses that extend, components that have safety margins, and a next generation, that is most likely modular, that can provide base load support that can’t be provided with other technologies. Framatome and Areva learned that wind and solar are a vital part of energy production, but they can’t be turned on during a snowstorm and there must be base power support. Decommissioning of units that are not of the right pedigree will happen. Units that are of the right pedigree will get an extended life and will be improved to be better, safer, and faster. In 20 years, the next generation will come online.
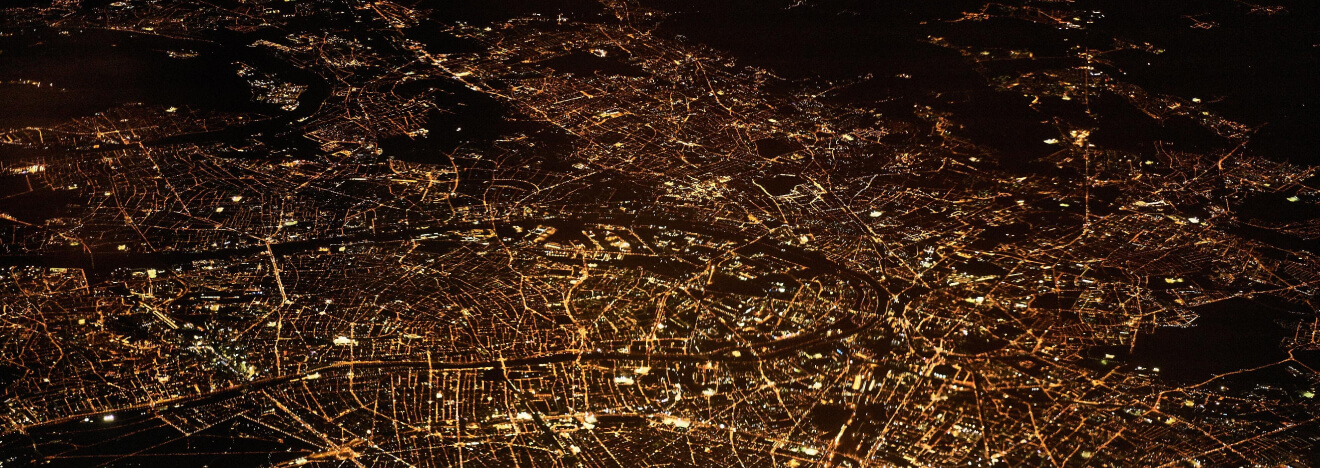