Ep 97: Craig Ranson - Senior Vice President, Installed Base America, Framatome (US)
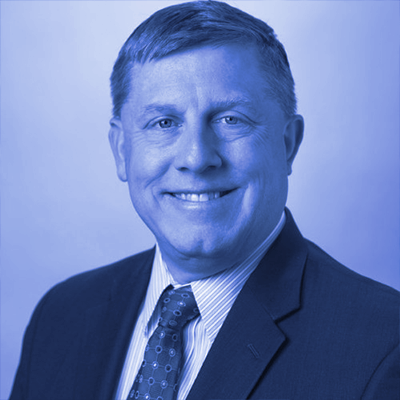
Show notes
1 - Intro to Nuclear Engineering
Bret Kugelmass: Did you grow up in the Northeast?
Bob Freeman: Bob Freeman grew up in downtown Boston and later received both his Bachelor’s and Master’s nuclear engineering degrees from the University of Massachusetts Lowell. Freeman had a strong aptitude for math and science, feeling a natural inclination to pursue engineering. Right after his first year, in 1985, Seabrook Station under a lot of pressure from the anti-nuclear groups. He didn’t understand what they were arguing and what was being covered in the media. A lot of the rhetoric didn’t fit the logic in Freeman’s mind, even lacking many facts and figures about nuclear at the time. He learned that a reactor core is approximately 12 feet in diameter, similar size to a gas truck. The gas would last one month for half the houses in the neighborhood, while the fuel in the reactor core would last two years. Nuclear has a number of different pathways within the industry, including service, operation, research, and vendors. He got his first job as a nuclear power plant and got his reactor license because of his experience working with his hands. They had a core that was high enriched uranium. Part of the Department of Energy (DOE) non-proliferation act was to take the high enriched uranium and move it down to low enriched uranium, leading to his focus on fuel.
2 - Design of a Nuclear Reactor Core
Bret Kugelmass: What form did the high enrichment fuel take?
Bob Freeman: The core was three feet high and three feet wide with flat plate type metallic fuel. The aluminum-uranium mix fuel was in high enrichment fuel was three inch by three inch squares making up the plates; eighteen flat plates were in the core. Bob Freeman worked on taking the uranium-aluminum core down to a uranium silicide type core matrix. The fuel was modeled in a computer and tracked neutron by neutron how it runs through the core, is multiplied, and absorbed. This was a Department of Energy (DOE) government program. There are ongoing efforts to develop nuclear fuel. Industry has made incredible strides with the existing technology of uranium dioxide in a zirconium rod. These rods are laid out in a matrix and the core tends to have around 50,000 fuel pins in a core, weighing in at 80-90 tons of material. By regulation, low enriched uranium is 0-5 weight percent. The ore out of the ground has a natural enrichment of 0.71 percent; the enrichment is driven high by replacing u-238 atoms with u-235 atoms, resulting in 5 percent. A mid-range of enrichment is between 5 to 19.75%. Anything about 19.75% is considered high enrichment; the fuel at Lowell at the time was 90.3% enrichment. A fuel design makes sure there is the right amount of poison control, which is used to control the reaction of neutrons, such as gadolinium. Different enrichments around the rod, radially and axially, allows the core power output to be designed.
3 - Path to Framatome
Bret Kugelmass: What is the advantage of having different levels of enrichment radially and axially throughout the reactor?
Bob Freeman: Having different levels of enrichment radially and axially throughout the reactor allows for different neutron flux. This allows burn out evenly among the 50,000 pins. At the end of the fuel cycle, one-third of the pins are replaced and the remaining are moved around to allow for even burn out, which allows the utility to create more power with less fuel. Bob Freeman left university and went to Combustion Engineering in Connecticut to do core design and shipping container design and licensing. He traveled to St. Louis, Missouri to analyze fuels and physics environments for the manufacturing plant. Freeman stayed with Combustion Engineering until the consolidation, choosing Framatome due to a similar culture, which was very employee friendly and customer focused. It is a symbiotic relationship between the vendor, utility, regulator, and Department of Energy. Freeman’s first role at Framatome was a licensing engineer and was shortly after put in charge of licensing and environmental health safety for Framatome and Siemens Power Corporation. Following that, Freeman became plant manager of the Framatome manufacturing plant. The plant is very high tech with a big focus on tolerance and quality. The UF6 (uranium hexafluoride) gas is converted into powder, which is pressed into ceramic pellets. The pellets are baked in furnaces and are individually controlled by barcodes, batches, and lots, similar to a chemical plant.
4 - Role of a Nuclear Fuel Vendor
Bret Kugelmass: How do you tell what level enrichment the fuel is at during production?
Bob Freeman: Material comes in based on laboratory results and it is converted from uranium hexafluoride into uranium dioxide, measured again as a powder, measured again as a pellet, and then the final rod is measured before it goes into the assembly to make sure there is a full quality assurance record for each rod. During fuel fabrication, the pellet is pressed, goes into a furnace where it is baked and hardened, and then goes through a grinder for shaping. The pellet is inspected before it is inserted into the rod, which is then welded on both ends. After another inspection, a scanner will check final enrichment. The rods are placed in a cage, where different measurements on the fuel assemblies can be made. Around 2011, Bob Freeman moved from working in manufacturing and special assignments into the development and commercial side of the business. He wanted to get closer to the customers, normally interfacing with the vice president of fuel or fuel director of different utilities, since they know the core requirements and outputs of their plants. The development of accident tolerant fuels and Framatome’s venture with Lightbridge, Enfission, takes the conventional fuels and advancing it into a whole other level which impacts the safety and economics of the plant. Chernobyl, Three Mile Island, and Fukushima had one thing in common: the reaction between zirconium and steam. Zirconium and steam separate the water molecule; the oxygen goes with the zirconium molecule and the hydrogen is left alone, causing a hydrogen explosion. Freeman worked with a plant in California to set up their fuel cycle to move from 18 months to 24 months alternating, allowing one plant to be up during the refueling of the other and the same crew to be brought in for each outage, saving money overall.
5 - Nuclear Fuel Purchasing
Bret Kugelmass: How long does a fuel contract last?
Bob Freeman: The smallest fuel contract is around four years, if something goes wrong. A typical fuel contract is about a decade, with the fabrication generally at a contracted price. Nuclear fuel has different elements, including the commodities of the uranium and enrichment, which is purchased independently at market price. Fabrication is the other element which takes the commodity and puts it in the fuel. The buyer, which is the utility, buys the commodity and has it shipped to the fabricator’s site. A small portion of buyers have switched their fuel supplier from the plant manufacturer, but they may do so if they find a better price or product. There are a number of activities going on in the industry to counteract some of the policies set around the United States. Each state has its own approach to energy. Framatome’s job is to help utilities survive; the best way to do that is with advanced technologies with better economics. They bring the technology and service part to verify that the reactor will operate reliably without shutdown. The cheaper nuclear fuel can be brought to the plants, the better it will counteract natural gas. Framatome also looks at ways to better harness the energy in the fuel.
6 - Accident Tolerant Fuel Development
Bret Kugelmass: What is the fundamental limit on how much you can burn up the amount of fuel in the uranium?
Bob Freeman: There is no fundamental limit on how much you can burn up the amount of fuel in the uranium, but it is based on the requirements of the time and the physics of the material. The Nuclear Regulatory Commission (NRC) has barriers on fuel burn up based on materials that have been submitted for approval. The burn up limit is a little outdated, which vendors are challenging. Getting the regulator to agree to raising the limit can be done through testing, demonstration, and analytics. The cladding and the pressure inside the fuel rod, released from the pellets, are the limiting factors. The zirconium alloy tube is under heavy neutron irradiation for two year cycles, up to six years. Industry is trying to determine pickup of hydrogen in the cladding. If hydrogen pickup and corrosion can be limited, the metal will last longer. A near term target for accident tolerant fuels (ATF) takes a detailed process of 30 different multilayer configuration coatings to be placed over the zirconium rod. Chromium was settled as the best. The uranium pellet is doped with chromium to get better properties for heat transfer. The rod is coated with a very tiny level of chromium. This plating stops the degradation and the reaction between the zirconium and steam. The nuclear industry is very risk averse, which throttles the speed of bringing advancements to market. The NRC looks judiciously at a new fuel for safety without a vested interest in whether it comes to market. The near-term solution for ATF’s is the chromium doping. The longer-term technology for ATF’s is silicon carbide, which is a ceramic composite fiber layer that is not zirconium. This would replace zirconium as the cladding, but there are technological barriers that must be managed. Lightbridge introduced a new technology to Framatome a year ago asking for a partnership. They created the joint venture, Enfission, which takes the base technology of the fuel rod and makes it into a metallic matrix. This gives the reactors a 10% power upright, operates at 1000 degree Centigrade less temperature in the centerline, and substantially less pressure drop across the core. Lightbridge brings a substantial economic and safety game change that is very promising.
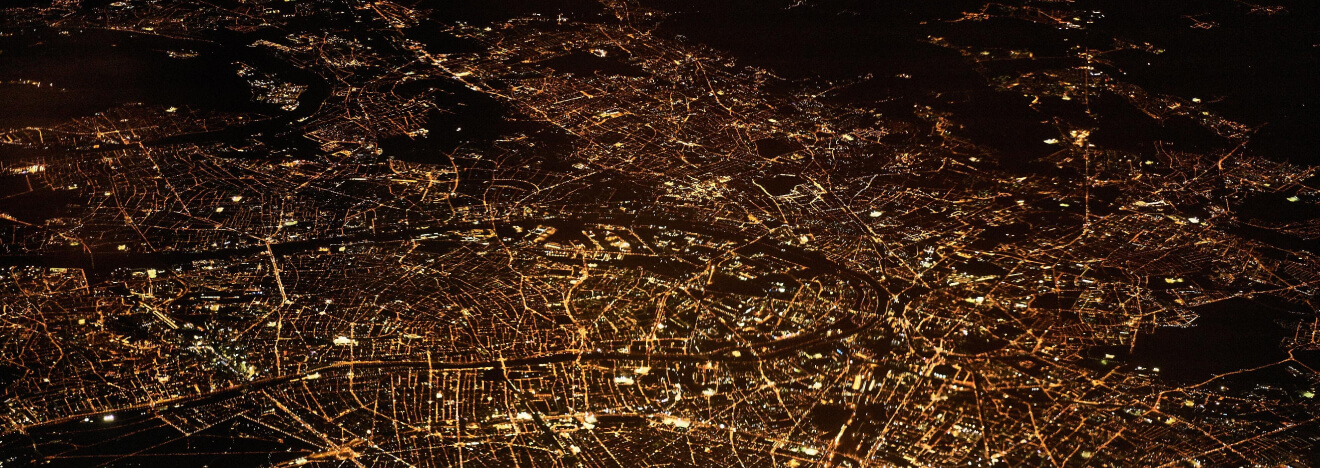