Ep 66: Charles Carpenter - Senior Technology Officer, Nuclear Advanced Manufacturing Research Center
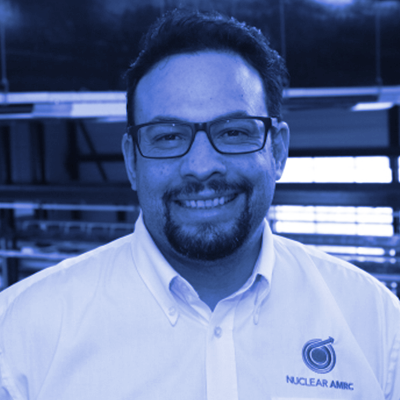
Show notes
Q1 - Heat Transfer in the Forging Process
Bret Kugelmass: Where are you from?
Charles Carpenter: Carles Carpenter is from Lovelock, Nevada and grew up during a time in which Yucca Mountain was getting ready to become a geological disposal area for the U.S. Residents in Northern Nevada, mostly towns centered around farming and mining, recognized benefits of the Yucca Mountain project such as the economics, rail structure, and research opportunities. Carpenter focused on heat transfer during his studies at the University of Nevada Reno (UNR). After graduation, Carpenter worked for Firth Rixson, a forging company, in the quality assurance department. Forging impacts almost every major industrial sector around the globe. Forging uses mechanical work and heat and temperature to push material into a desired shaped with certain properties. Carpenter completed a lot of titanium-based alloys, which are alpha beta processes. While working for Firth Rixson, a lot of the work was specialized in titanium alloys and super nickel alloys for the aerospace industry and land based turbines. For the nickel based alloys, high temperature and creep resistance were the main concerns and were controlled by grain size and metallurgical properties. During his time in quality assurance, Carpenter worked in heat treatment, which is a special process that must be performed to achieve specified properties. Higher temperatures allow you to forge and press the material into a certain shape and size, but as you get closer to the desired properties, certain temperatures are better based on the end product. Tempering and annealing softens the material for the machining process. Carpenter returned to UNR and received his master’s degree in mechanical engineering. He worked on the sintering process for two phase heat transfer, which is taking a powder and heating it up to near its melting point.
Q2 - Heat Transfer and Logistics Background
Bret Kugelmass: What temperature is two phase heat transfer completed at?
Charles Carpenter: Charles Carpenter completed experiments with two phase heat transfer during his master’s program, mostly for boiling water at atmospheric pressure, but with other variances added into the experiments. After receiving his master’s in mechanical engineering at the University of Nevada Reno, Carpenter took a logistics role in quality assurance at Aero Electronics. The focus in this logistics environment is not on controlling the specific product, but instead creating a process that produces the desired product at the end. Carpenter got married to a previous Firth Rixson coworker, who was originally from Sheffield in the U.K. After doing logistics for a while, Carpenter decided to move to the U.K., first volunteering at a recycling plant with mentally handicapped adults who worked there. This was an eye opening opportunity for Carpenter to learn about human factor challenges. He learned that everyone in a workforce has different needs and needs different tools to complete what they need to do.
Q3 - Welding Manufacturing Processes
Bret Kugelmass: How do people change a manager’s strategy and technique?
Charles Carpenter: Charles Carpenter sees the industrial setting as sometimes easy to forget that people and roles need to be differentiated. After volunteering at the recycling center, Carpenter travelled around Sheffield to look for jobs. He happened upon the Nuclear Advanced Manufacturing Research Centre (NAMRC), discovering that it looked like a university-type lab environment. He applied to the center and realized it was much bigger than the university-type lab he expected and considered it somewhere worth being. Carpenter’s first role at the NAMRC was as a project manager for welding, spending most of his time in tube sheet welding, which has a lot to do with heat exchangers and steam generators. One of the challenges was how to move tube sheet welding to a more automated process. Carpenter also worked on developing the manufacturing process for this operation. Orbital welding equipment has mandrels that go into the tubes, centers itself, and has an orbital component that can weld all the way around the tube. This is a semi-automated process, as a person still needs to move the equipment from tube to tube and make sure the equipment and material is clean. Carpenter also worked on designing experiments to determine requirements to achieve the desired weld output and identify the inputs that have the most impact on the outputs.
Q4 - How New Manufacturing Processes are Developed
Bret Kugelmass: What’s the result of a welding process development?
Charles Carpenter: Ideally, if there is a welding process that needs to be developed, a customer brings the need forward and accepts the new process on-site to train their operators. Charles Carpenter was recently involved with the machining the nozzles of a new reactor pressure vessel (RPV) head. The team needed to understand how tools, especially milling tools, wear out and determine which type of machining strategy would be used. These processes are proved out on the NAMRC machines, so when it is transferred to the customer, it’s fully programmed and ready to use. For the RPV nozzles, the NAMRC looks at about a 40 percent reduction in machining time and looking where it could be improved for machining wear and limiting cutting of fresh air. When the NAMRC develops new processes for a client, they get people from the customer’s side who will actually be involved in the process involved at the beginning to feel buy in and see the directions taken. For the tube sheet welding process, code requirements on hazardous fluids determined some of the direction taken. Early engagement also includes showing the customer why some paths are not taken in the development process. A positive handoff to the client is necessary, otherwise the research doesn’t get translated into the overall impact. Carpenter transitioned into a role as a senior technology officer. Other research centers are in place for other industries: aerospace, composite, forming and formulations, and biologic. Each site has a senior technology officer and they work collaboratively to identify common areas of interest, such as automation and digital manufacturing. Many challenges, such as quality assurance, are shared across industries.
Q5 - Future of Advanced Manufacturing in Nuclear
Bret Kugelmass: How do you overcome communication challenges with teams working at different sites?
Charles Carpenter: When Charles Carpenter first became a senior technology officer at the Nuclear Advanced Manufacturing Research Centre (NAMRC), he had to develop a way for people to start sharing information. They first set up technology forums, bringing in experts in metrology, automation, visualization, and met in groups once a quarter to talk about what they are doing in their technology. Then groups start talking to national bodies that are interested in the same things. The National Physical Laboratory is interested in the same things as the metrology group, because they are both looking at measurements. Cross center projects were developed to create funding avenue for common areas of interest between national bodies and industry. NAMRC is working towards large transformational projects, which is getting the larger partners and people more engaged. Small modular reactors and advanced modular reactors are progressing in nuclear. With modularization, it moves towards more factory type builds. As a factory, they consider the 1-3-8 model from the shipbuilding model. If it takes one hour to create in the factory, it takes three hours to fabricate on a dry dock and eight hours to fabricate at the pier. Technology is progressing to get as much fabrication in the factory. NAMRC has a lot of projects around automation, virtual reality and digital manufacturing. Single platform manufacturing minimizes the movement of products during the manufacturing phase, instead making work cells more flexible and versatile. Advanced manufacturing technologies, such as laser welding and electron beam welding, are growing and being used together, not just singularly. NAMRC is working on a project with the Electric Power Research Institute and the Department of Energy in the U.S. and NuScale to determine how the technologies can be combined to create a two-thirds replica of the NuScale reactor pressure vessel in twelve months.
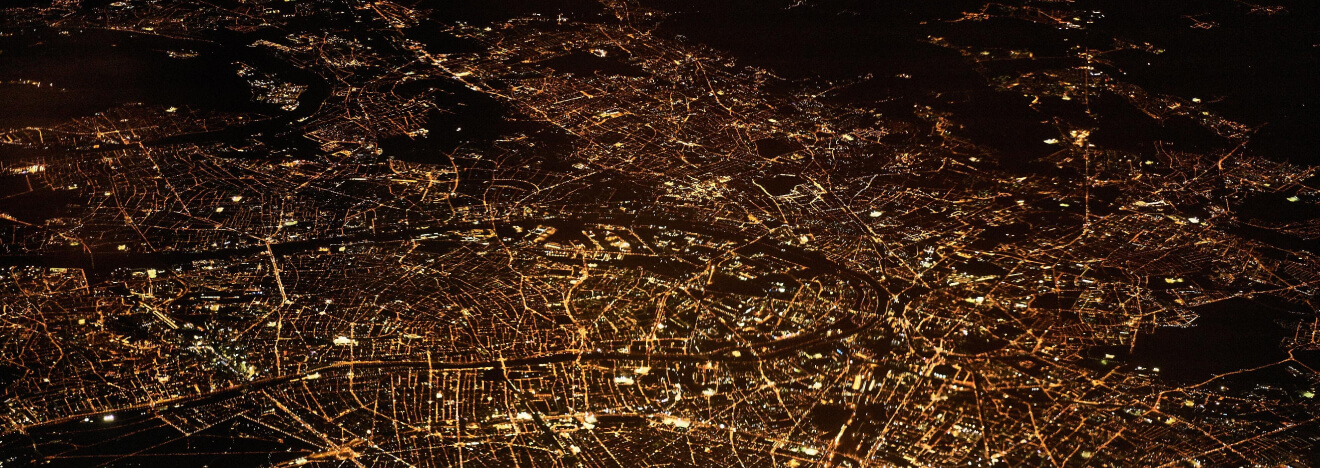