Ep 82: Aladar Csontos - Advanced Fuels Expert , EPRI
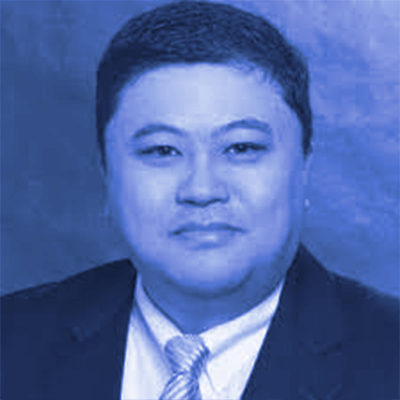
Show notes
1 - Path to Nuclear through Material Science
Bret Kugelmass: Where did you get started?
Aladar Csontos: Aladar Csontos studied material science at Johns Hopkins, specifically working on tank armor and tank material for his thesis. Tank material is magnetic and its properties can be changed and manipulated to look like it has a magnetic signature of a car. This was primarily a big issue in the late 1980’s and early 1990’s in Eastern Europe, because the mines would go after only tanks based on the magnetic signature. Aladar Csontos developed microscopy skills during this process and also during grad school at UVA. During grad school, Csontos also worked for Ethyl Petroleum Company and showed in the microscopy how nanoparticles of carbon were causing corrosion on diesel engine parts. If the agglomeration of the nanocarbon subparticles could be removed, the engine would be much longer lived. When Csontos went to the Electric Power Research Institute (EPRI), he learned about what it took in terms of the infrastructure cost, supply chain issues, and changes that come with innovation of a new material. Csontos spent 15 years at the Nuclear Regulatory Commission (NRC) before going to EPRI, spending some time at Yucca Mountain, transportation, and dry storage. Right after grad school, Csontos worked at the Center for Naval Analysis working out logistics issues related to Operation Enduring Freedom after 9/11. During this analysis, he realized that nuclear carriers didn’t need anything other than the jet gas for the airplanes, getting him thinking about how much gas money was saved. This peaked Csontos’ interest in nuclear and Yucca Mountain had a great public service aspect to it, looking at how to store and dispose of waste safely. Csontos started working on canisters and the engineered barrier system at Yucca Mountain.
2 - Degradation Phenomena at Yucca Mountain
Bret Kugelmass: What are the engineered barriers at the Yucca Mountain site?
Aladar Csontos: Some engineered barriers at the Yucca Mountain site include the nickel alloy for the canisters and a drip shield. The Nuclear Regulatory Commission (NRC) has the role and responsibility to regulate the civilian uses of nuclear materials. The Department of Energy (DOE) is responsible for licensing the repository. Al Csontos worked on the regulatory side of ensuring the repository at Yucca Mountain would safely operate. While at Yucca Mountain, Csontos also looked at the safety of piping with degradation and how to manage degradation. He worked closely with folks from the Electric Power Research Institute (EPRI) who were evaluating different degradation phenomena, such as stress corrosion cracking, pitting, and crevice corrosion. This was a large area of research called the Materials Initiative that occurred over a 15 year period. Stress corrosion cracking is a combination of electrochemical corrosion plus stresses that allow a crack to grow. The combination of stress corrosion cracking and pitting in canisters for dry storage was a concern and the degradation mechanisms had to be managed, such as chlorides on stainless steel. Salt has caused pitting and cracking on nuclear sites, as well. EPRI is working on how to inspect pits and cracks and how to mitigate against pitting. Management of long term storage of the dry cask storage systems has been a global problem. When two materials are in contact with each other and there is a layer of water in between and dissimilar metals, dissimilar corrosion of one kind or another can result.
3 - Accident Tolerant Fuel Development
Bret Kugelmas: Is there a focus on alloy development because new alloys have properties to resist phenomena that has been observed over time?
Aladar Csontos: Sometimes new alloys are developed; many locations that have alloy 600 reactor pressure vessel heads have moved to alloy 690 due to stress fracture cracking. Other areas don’t make material changes, but instead mitigate and repair. Spray technologies for coating surfaces with new metals is being looked at for stainless steel canisters. Cracking issues may be able to be mitigated by laser peening, which imparts a compressive residual stress on the surface of the canister. Al Csontos sees that many safety benefits are tied to economic benefits, such as the benefits of dry storage aging management. Al Csontos left the Nuclear Regulatory Commission (NRC) at a time in which he was concerned about the future of nuclear. An opportunity to work at the Electric Power Research Institute (EPRI) in the area of accident tolerant fuels and Csontos was highly interested in pursuing the subject due to his desire for public service and the recent Fukushima incident. Accident tolerant fuels are fuel concepts that will reduce the probability or coping times from an event like Fukushima or a meltdown. If fuels could be more resilient and robust, there is more time to address an emergency situation. EPRI has done more analysis of other types of design basis accidents and anticipated operational occurrences, which are scenarios that the NRC requires vendors to look at for their fuel capabilities. Accident tolerant fuels are now called advanced technology fuels (ATF). ATF’s provide an extra one to three hours of benefits. One concept is coated cladding. A normal zirconium fuel is coated with chromium, which is more resistant to failure and can operate at higher temperatures.
4 - Economic Benefits of Minimizing Oxidation
Bret Kugelmass: What temperature does oxidation start at?
Aladar Csontos: Oxidation occurs all the time, including rust and corrosion. Rapid runaway oxidation occurs at a much higher temperature. By putting a chromium coating on the zirconium, it doesn’t oxidize as fast and at higher temperatures. If the fuel can be left in the reactor longer, there are economic benefits. If the enrichment and burnup can be slightly raised, the intervals can be extended to two years and another cycle can be added in the fuel life. One study the Electric Power Research Institute (EPRI) completed in 2005 showed that there are benefits to going to two year intervals and the industry is interested in going towards this goal. Chromium oxide is very hard and, based on current observation, acts like a very good protector against debris damage. Right now, the Nuclear Regulatory Commission (NRC) has approved the underlying layer, the zirconium fuel rod bundle. Putting an additional layer increases safety, not decrease, but there is still a question about delamination. Hatch Southern Nuclear has placed in two types of advanced technology fuel (ATF) concepts. One is an oxide coating, a ceramic armor coating. Small segments of fuel rods have been placed into Hatch to see how it reacts and how it operates during normal operations. A ferritic steel, iron chrome aluminum alloy, was also placed inside to see how it would respond under normal conditions.
5 - Advanced Materials in Advanced Technology Fuels
Bret Kugelmass: Are there other types of approaches in advanced technology fuels (ATF)?
Aladar Csontos: Some advanced technology fuels (ATF) focus only on the cladding. Inside a fuel rod, there is a stack of uranium dioxide fuel pellets inside a zirconium rod. This zirconium alloy has been optimized over the past 35 years and fuel vendors have created a very good fuel. The Electric Power Research Institute (EPRI) is looking into how fuels can be made more cost effective in terms of efficiency and cost benefit analysis. The Department of Energy (DOE) funded the development of these concepts after Fukushima and has focused on three different concepts: coatings, ferritic steel, and a silicon carbide concept with a different fuel pellet, a uranium silicide fuel that has more uranium atoms, which allows for more power. Another concept, Lightbridge, is a metallic fuel that has a twisted cruciform shape, which increases conductivity. The focus of Lightbridge is on the current fleet, but also in the next generation of reactors. EPRI is looking at how to bring technologies to market faster. The traditional fuel development time has been 20+ years. The Nuclear Regulatory Commission (NRC) needs to know what the product will be able to withstand for a safety argument to the public. A lot of tests need to be performed across many different parameters and in different conditions, including irradiation of materials and post-irradiation exams. There may be ways to collect data in-line or while it’s being tested or operated to make sure no limits are encroached on. Advanced sensors and advanced non-destructive examinations interrogate the fuel assemblies and fuel rods to make sure they are operating safely. There needs to be more regulatory certainty or understanding of longer term concepts that have greater value.
6 - Nuclear Fuel Development Process
Bret Kugelmass: What is the shortest period of time to go from concept to implementation of new fuel utilizing new techniques?
Aladar Csontos: Using new techniques, a new fuel could go from concept to implementation in less than ten years. There may be ways to do advanced modeling ahead of time to get at some of the materials issues beforehand to predict how the material will behave, so research and development should focus on advanced modeling. With advanced non-destructive evaluation (NDE) and advanced sensors, a predictive framework can come together to provide health monitoring of the fuel. Development of the coatings itself can be done in a very short timeframe. There are a lot of test reactors internationally and domestically. The Department of Energy (DOE) has the advanced test reactor (ATR) at the TREAT facility. Accelerated testing aims to show how materials and properties change over time. This data can be used to predict how the fuel will perform long term for the different cycles. A lot has been learned from reactor operations over the past 60 to 80 years. The Electric Power Research Institute (EPRI) has a big role in certain areas like water chemistry, since they create the guidelines. The fuel development process is iterative and sequential. Going from fuel lead test rods (LTR’s) to assemblies to a couple of assemblies to a batch of assemblies in sequence increases the level of confidence. Aladar Csontos is optimistic about advanced fuels. Nuclear is cost effective because of the low cost of fuel. There is an opportunity to increase the efficiency on the cost side of the fuels even more, in fuel cycle optimization. In the future, coated fuel rods will bring safety, more enrichment and burnup will bring efficiency, and longer cycle times will allow power to be generated for longer periods of time. Resilient fuels may be able to work better with solar, wind, and hydro, which could be a long term benefit to the U.S. energy portfolio.
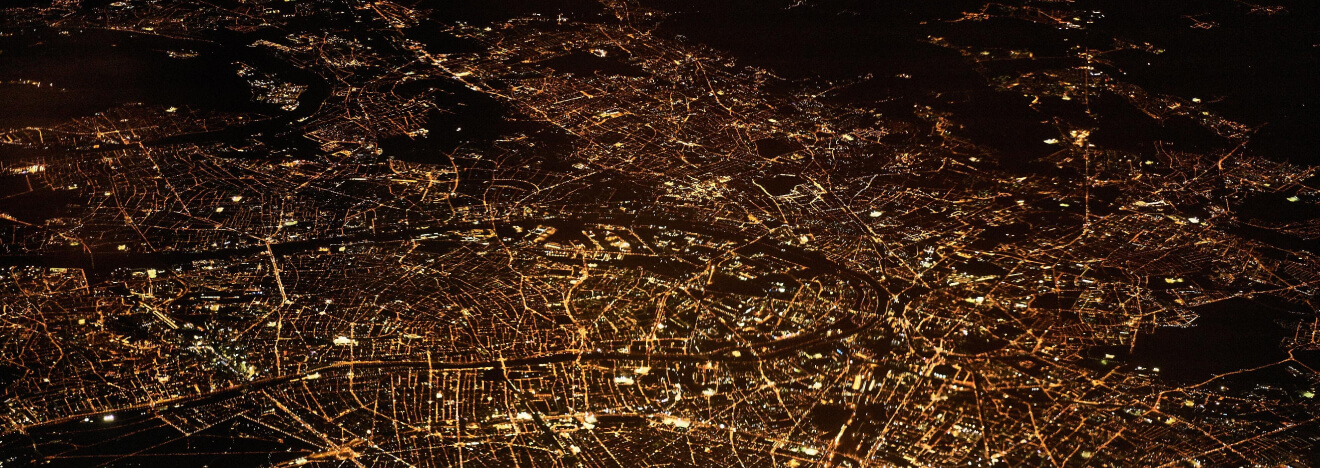